Capítulo 3
Medidas para Sistemas Acionados a Motores Elétricos
O consumo de energia elétrica na indústria é essencialmente devido à utilização de equipamentos que convertem energia elétrica em mecânica (motores elétricos). Para estes existem soluções de motores de alta eficiência cuja seleção deverá ser fundamentada numa análise custo/beneficio, no entanto, sempre que possível, deverão ser instalados variadores de velocidade que permitam adaptar o funcionamento do motor às necessidades específicas do processo. Como casos particulares de aplicação de motores elétricos, podemos referir os sistemas de bombagem utilizados habitualmente no transporte de líquidos, os sistemas de ventilação e compressão usualmente aplicados a transporte de gases e finalmente os transportadores de sólidos. Para cada um destes sistemas são apresentadas as melhores práticas, procurando-se encontrar as soluções ótimas quer em termos de operação, quer em termos de configuração.
3.1 Motores Elétricos
Os motores elétricos efetuam a conversão de energia elétrica, recebida da rede, em energia mecânica. De todos os tipos de motores, os motores elétricos são os mais usados, pois combinam as vantagens de utilização de energia elétrica – facilidade de transporte, limpeza e simplicidade de comando com a sua construção simples e uma grande versatilidade de adaptação às diferentes cargas 20.
Os motores elétricos desempenham um papel fundamental na indústria, o que se reflete igualmente num peso elevado nos custos energéticos associados ao seu funcionamento. Em Portugal, são responsáveis por 70% do consumo de eletricidade da indústria 21.
A Figura 3.1 apresenta o consumo de eletricidade dos motores, pelas principais utilizações finais na Indústria Portuguesa.
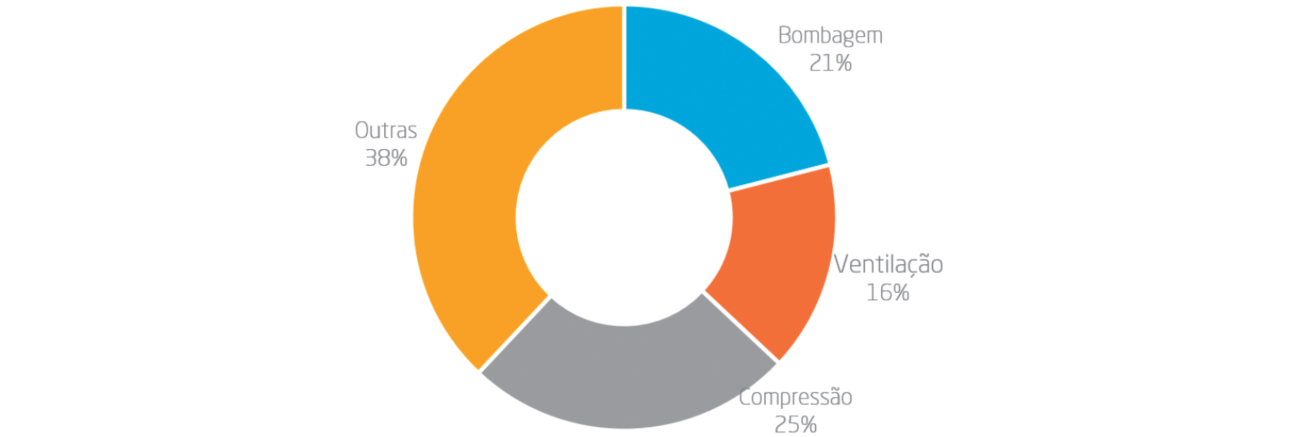
Figura 3.1 – Consumo de energia dos motores elétricos na Indústria Portuguesa 22
Como se pode verificar, as aplicações em que ocorre movimentação de fluidos representam 62% do consumo elétrico total dos motores industriais.
Os motores elétricos podem ser alimentados com corrente contínua ou alternada. Os motores elétricos com corrente alternada podem ser divididos em duas categorias: síncronos e assíncronos (ou de indução).
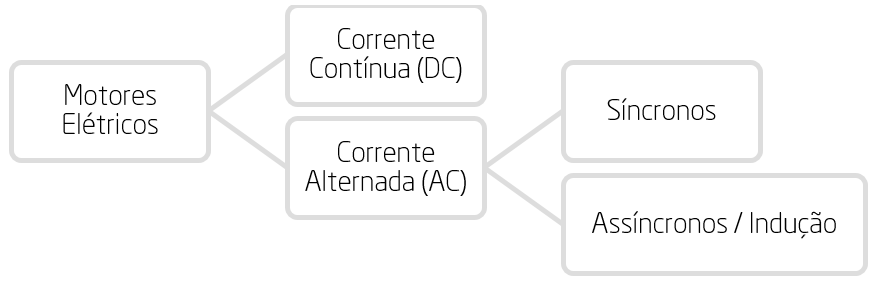
Figura 3.2 – Classificação de motores elétricos
Os motores síncronos funcionam com velocidade fixa. Utilizam um circuito induzido que possui um campo constante pré-definido e com isso aumentam a resposta ao processo de arrasto criado pelo campo girante. São geralmente utilizados quando são necessárias velocidades estáveis, com cargas variáveis, ou para grandes potências, com um binário constante.
Os motores assíncronos ou de indução funcionam normalmente a uma velocidade constante que varia ligeiramente consoante a carga mecânica aplicada ao eixo. Devido à sua simplicidade, baixo custo e manutenção mínima são os motores mais utilizados. Ocorrem em várias aplicações, tais como bombas, ventiladores, compressores de ar, misturadores, tapetes rolantes, etc.
Embora o motor elétrico tenha sido corretamente dimensionado e funcione em condições adequadas, existem perdas térmicas que habitualmente provocam aumento de temperatura no motor.
De forma a aumentar a eficiência dos sistemas de potência industriais têm sido desenvolvidas e aplicadas várias tecnologias que incluem motores elétricos de alto rendimento, os variadores eletrónicos de velocidade (VEV) ou a otimização dos sistemas de transmissão mecânica entre o motor e o equipamento final.
A eficiência dos motores elétricos é um tópico fundamental, devido ao elevado custo da energia elétrica. O facto de os motores elétricos terem um consumo elevado de eletricidade, e de existirem tecnologias que permitem aumentar a sua eficiência energética, tornou a aplicação de motores elétricos numa área com possíveis economias energéticas bastante significativas.
3.1.1 Otimização de Motores
A transformação de energia elétrica em mecânica acarreta sempre perdas, como se verifica pelo esquema da Figura 3.3.
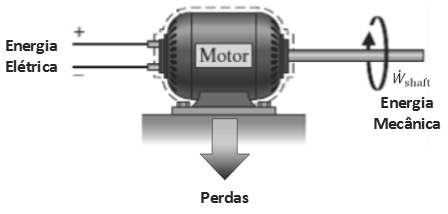
Figura 3.3 – Balanço energético simples a um motor elétrico
As perdas, que são inerentes ao processo de transformação, são quantificadas através do rendimento. O rendimento de um motor, η, é igual à potência mecânica, Pmec, disponível no veio do motor a dividir pela potência elétrica, Pel, fornecida ao motor:

As perdas não só contribuem para a redução do rendimento do motor, como também vão provocar um aumento da temperatura do motor, o que levará a uma redução do tempo de vida útil do motor.
As perdas num motor de indução podem dever-se aos efeitos descritos em seguida 20:
- Perdas no cobre por efeito de Joule – devem-se à passagem da corrente nos enrolamentos do estator e na gaiola do rotor. São proporcionais ao quadrado da corrente e ao valor da resistência;
- Perdas magnéticas no ferro – estão associadas à variação no tempo do fluxo magnético, produzindo correntes induzidas no ferro e perdas por histerese. São proporcionais ao quadrado da densidade do fluxo magnético;
- Perdas mecânicas – resultam do atrito nos rolamentos e da ventilação do motor;
- Perdas extraviadas – ou perdas suplementares, estão associadas a imperfeições no fabrico, às irregularidades na densidade de fluxo magnético no entreferro e à distribuição não uniforme da corrente nos condutores.
As medidas para a otimização da eficiência energética dos motores elétricos e sistemas de potência associados têm como objetivo a minimização das perdas energéticas inerentes. Neste âmbito, as medidas seguintes encontram-se entre as mais efetivas:
- Substituição de motores convencionais por motores mais eficientes;
- Utilização de VEV;
- Utilização de arrancadores suaves para evitar picos de corrente durante o arranque;
- Garantir a manutenção adequada dos motores;
- Evitar o sobredimensionamento dos motores e desligar os mesmos quando estes não estão a ser utilizados.
3.1.2 Substituição de Motores Convencionais por Motores mais Eficientes
Os motores de alta eficiência apresentam perdas, em geral, inferiores a 30-50% relativamente aos motores standard.
A melhoria de rendimento obtida para os motores de alta eficiência situa-se normalmente nos 3-4%, podendo, no entanto, atingir um valor máximo de 8% 20.
Os motores de alto rendimento, por terem menores perdas, funcionam normalmente a mais baixa temperatura, o que conduz a uma vida útil mais longa. Há, contudo, aspetos menos positivos no funcionamento de um motor de alto rendimento, que são causados pela menor resistência do rotor.
O Comité Europeu de Fabricantes de Máquinas Elétricas e de Sistemas Eletrónicos de Potência (CEMEP) e a Comissão Europeia estabeleceram, em 1998, um esquema de etiquetagem da eficiência do motor aplicado a motores trifásicos de indução de 2 ou 4 polos (400 V, 50 Hz, classe de funcionamento S1), com gamas de potência entre 1,1 e 90 kW. O esquema de etiquetagem CEMEP-CE estabelece 3 classes de rendimentos que se encontram descritos na Tabela 3.1.
Tabela 3.1– Classificação CEMEP-CE da eficiência de motores elétricos.

A Figura 3.4 mostra para a gama de potência, os domínios de eficiência dos motores das classes EFF 1, EFF 2 e EFF 3.
![Figura 3.4 – Eficiência vs. potência útil para motores das classes EFF1, EFF2 e EFF3 de acordo com o esquema de etiquetagem CEMEP-CE [23]](/sites/default/files/inline-images/figura-3.4.png)
Figura 3.4 – Eficiência vs. potência útil para motores das classes EFF 1, EFF 2 e EFF 3 de acordo com o esquema de etiquetagem CEMEP-CE 23
Com base na Figura 3.4, a Tabela 3.2 apresenta, para vários motores de 4 polos com diferentes potências úteis e para um período de funcionamento de 4000 h/a, os valores mínimos de economia energética possíveis de obter através da substituição de motores de classe EFF 3 por motores de classe EFF 1.
Tabela 3.2 – Economias energéticas obtidas por substituição de motores de classe EFF3 por motores de classe EFF1.Valores calculados para motores com diferentes potências úteis e para um período de funcionamento de 4000 h/ano
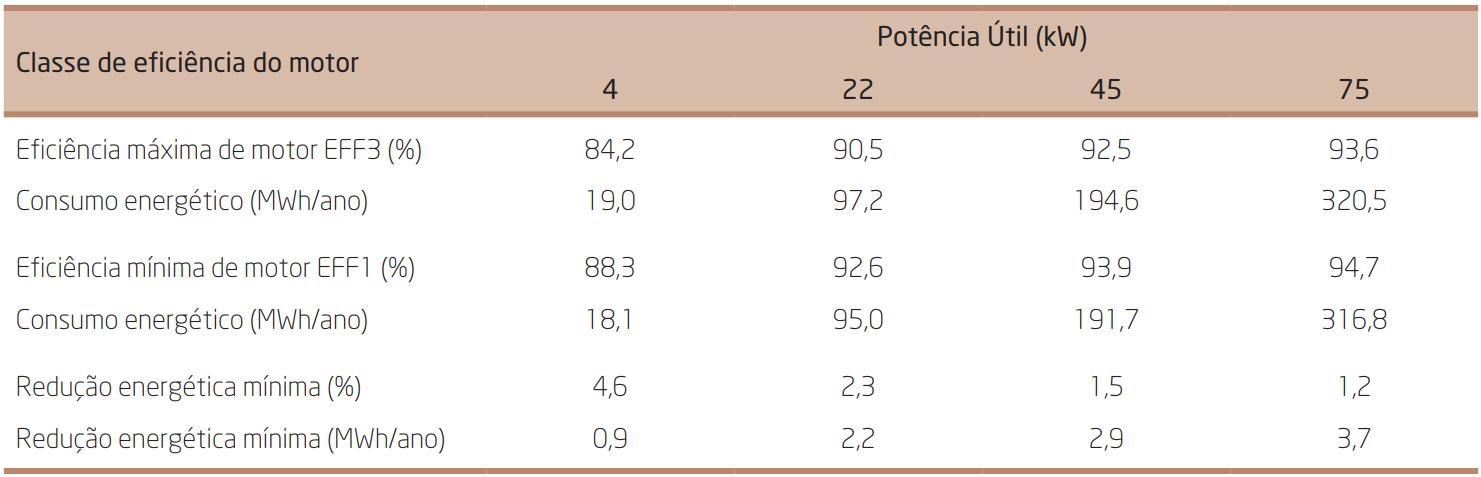
Apesar de serem energeticamente mais eficientes e por essa razão mais económicos em termos operacionais, os motores de alta eficiência, são motores que exigem um investimento inicial cerca de 25 a 30% superior em relação aos motores convencionais. Devido ao acréscimo de custo de investimento, é aconselhada a realização de uma avaliação prévia técnico- -económica global do investimento através de uma análise custo-benefício.
A avaliação económica do investimento ligado à substituição de um motor convencional por um motor de alta eficiência é feita através do cálculo do tempo de recuperação do investimento. Para tal usa-se a Equação (3.2).

Em que a poupança anual é dada pela Equação (3.3):

onde: t é o número de horas de funcionamento do motor num ano, Cel é o preço médio da eletricidade (€/kWh), Pst é a potência útil mecânica do motor standard (kW), PMAE é a potência útil mecânica do motor de alta eficiência (kW), ηst é o rendimento do motor standard e ηMAE é o rendimento do motor de alta eficiência.
A substituição de um motor convencional por um motor de alta eficiência é na maioria dos casos justificada, sendo o investimento amortizado em 1 a 2 anos para períodos de funcionamento à volta das 4000 h/ano, e em cerca de 3 anos para 2000 h/ano de funcionamento.
3.1.3 Utilização de Variadores Eletrónicos de Velocidade (VEV)
Vários estudos apontam para a utilização de VEV, como a medida com maior potencial de poupança em sistemas motorizados devido ao papel extremamente importante na redução dos consumos de energia. Almeida et al 2005 24 apresenta os resultados de uma investigação a nível europeu sobre as considerações técnicas e económicas de aplicação de VEV a sistemas motorizados e tem sido um documento de referência sobre esta matéria.
Na indústria em Portugal, o sobredimensionamento de motores de indução é uma situação muito frequente, devido à utilização sistemática de fatores de segurança muito elevados. O sobredimensionamento excessivo conduz a três desvantagens principais:
- Investimento inicial superior na aquisição do motor e na aparelhagem de comando e proteção do motor;
- Degradação do rendimento do motor, conduzindo a maiores custos de funcionamento da instalação;
- Degradação do fator de potência da instalação, com o consequente aumento dos custos na fatura elétrica ou na necessidade de aquisição de equipamentos para compensar o fator de potência.
Por conseguinte, seria muito benéfico para a maioria das aplicações se a velocidade do motor se ajustasse às necessidades. A velocidade dos motores de indução é determinada pela frequência da tensão de alimentação, pelo seu número de polos e pelo seu fator de carga. Deste modo para controlar a velocidade dos motores é necessário variar a frequência da tensão de alimentação.
Os VEV, normalmente, convertem a tensão da rede de 50 Hz numa tensão contínua e em seguida sintetizam uma frequência variável sob controlo externo do utilizador que pode ir de 0 a 400 Hz. Existem diversos tipos de configurações do circuito eletrónico dos VEV, consoante o tipo de motor e a gama de potência.
Os VEV com inversor por fonte de tensão e modulação por largura de impulso são os que mais se utilizam para o controlo de motores de indução. Este tipo de VEV é basicamente constituído por um retificador (controlado ou não controlado) que converte a tensão alternada em contínua e por um inversor que converte a tensão contínua em alternada.
3.1.3.1 Aplicações dos VEV
As principais aplicações dos VEV são para o acionamento de bombas, ventiladores e compressores, onde se pode encontrar o maior potencial para conservação de energia.
Os caudais de fluido necessitam de ser reguláveis ao longo do processo, pelo que são utilizados dispositivos de estrangulamento (válvulas reguladoras de pressão (throttles) e amortecedores de pulsações/vibrações (dampers). Embora contribuam para as funções desejadas, os dispositivos fazem-no à custa de introdução de perdas de carga no sistema, desperdiçando quantidades consideráveis de energia.
A implementação de VEV é aconselhada para os motores elétricos que funcionam numa carga variável a menos de 50% da capacidade durante pelo menos 20% do seu tempo de funcionamento e no minimo durante 2000 horas por ano.
As principais vantagens da aplicação dos VEV a motores elétricos na indústria, são:
- Economias de energia até 50%, com um valor médio entre 20-25%;
- Redução/limitação de picos de corrente durante o arranque e paragem do motor;
- Prolongamento da duração do motor;
- Aumento da produtividade;
- Capacidade de by-pass em caso de falha;
- Melhoria do processo de controlo e da qualidade do produto e/ou serviço;
- Diminuição da quantidade de partes mecânicas, dado o caráter compacto dos VEV e estes incorporarem já diversos tipos de proteções para o motor (contra curto-circuitos, sobreintensidades, falta de fase, etc.) que deixam assim de ser adquiridas isoladamente.
3.1.3.2 Análise económica da instalação e utilização de um VEV
Os variadores eletrónicos de velocidade têm vindo a tornar-se atrativos do ponto de vista económico. A melhoria do desempenho e fiabilidade dos VEV fornece maiores reduções dos consumos energéticos e acelera a amortização dos investimentos associados à sua instalação e utilização, diminuindo dessa forma o tempo de recuperação do investimento.
A rentabilidade dos VEV depende da potência do motor a controlar e do tipo de aplicação. No entanto, existem outros fatores importantes: (i) número de horas de funcionamento; (ii) regime de carga do motor. Em relação a este último fator, quanto mais variável for o regime de carga, maior será o potencial de economia de energia.
Para estudar a viabilidade económica da instalação de um VEV num determinado motor de indução, é necessário contabilizar o rendimento global considerando os vários regimes espectáveis. Se por um lado o controlo da velocidade pode permitir uma diminuição do consumo de energia bastante significativo em determinados regimes de carga, o facto de tal ser conseguido através de um dispositivo que introduz consumos adicionais, pode levar a poupanças negativas noutros regimes de carga 25.
Assim, considerando a existência de i regimes de carga, a poupança anual total resultante da implementação de um VEV num motor elétrico inicialmente sem controlo de velocidade, é dada pela Equação (3.4).

onde:
i – índice correspondente ao regime de carga;
ti – número de horas de funcionamento do motor no regime de carga i (h/a);
Cel,i – custo médio de eletricidade durante o período (€/kW.h);
PM,i – potência mecânica útil do motor no regime de carga i (kW);
PVEV - M,i – potência mecânica útil do motor com VEV no regime de carga i (kW);
ηM,i – rendimento do motor no regime de carga i;
ηVEV - M,i – rendimento do motor com VEV no regime de carga i
3.2 Sistemas de Bombagem
Os sistemas acionados por motores elétricos são responsáveis por cerca de 2/3 do consumo de energia elétrica no setor industrial da União Europeia. Em Portugal este valor é superior, representa 77% do consumo de energia elétrica na industria 22. Os sistemas de bombagem são muito importantes a nível industrial, representando cerca de 21% do consumo elétrico da Indústria Portuguesa, tal como apresentado na Figura 3.1.
A importância dos sistemas de bombagem na indústria deve-se essencialmente ao seu número. De facto, como muitas unidades industriais têm centenas destes sistemas, o primeiro passo para aumentar a eficiência energética envolve a identificação dos sistemas que têm maiores perdas, tornando-os alvo de planos de otimização. Estes planos devem envolver os seguintes passos 26:
- Avaliar todos os sistemas de bombagem e identificar aqueles que necessitam de ser rapidamente melhorados;
- Analisar detalhadamente os sistemas identificados;
- Desligar bombas desnecessárias ou usar interruptores de pressão de modo a controlar o número de bombas em funcionamento;
- Repor as folgas internas das bombas;
- Substituir ou modificar as bombas sobredimensionadas;
- Instalar VEV ou usar arranjos com múltiplas bombas (p. ex., bombas em paralelo) para garantir uma variação de caudal sem recorrer a válvulas reguladoras de caudal;
- Substituir os motores elétricos convencionais por motores de alta eficiência;
- Reparar fugas e válvulas deficientes;
- Estabelecer um programa de manutenção periódico.
Numa etapa inicial deverá ser efetuada a listagem dos principais problemas associados à seleção/dimensionamento e manutenção de bombas e respetivas medidas a implementar para solucionar esses problemas.
Os principais problemas apontados podem ser resumidos em cinco grupos:
- Excessiva manutenção de bombas. Este problema pode indicar: a) bomba em cavitação; b) bomba envelhecida; c) bomba não adequada à operação em causa;
- Excesso de estrangulamento na descarga. Uma bomba estrangulada para carga na sucção, com carga e caudal constante, significa um excesso de capacidade;
- Uma bomba com ruído geralmente indica a existência de cavitação. As válvulas de controlo ou de desvio de caudal (by-pass) que provocam ruído indicam, frequentemente, a existência duma queda exagerada de pressão;
- Alterações nas condições de projeto. Modificações nas condições de operação da instalação podem levar a situações de perda de eficiência;
- Bombas com sobredimensionamento desadequado. O sobredimensionamento provoca um desperdício de energia porque um determinado caudal é bombeado a uma pressão superior à exigida.
As medidas ou soluções a adotar para resolver esses problemas podem ser sintetizadas também em cinco grupos:
- Substituir bombas sobredimensionadas. As bombas sobredimensionadas são a maior fonte de desperdício de energia em sistemas de bombagem. A sua substituição deve ser sempre avaliada em relação a outros métodos possíveis para reduzir a capacidade (p. ex., mudança de impulsores e uso de VEV para o controlo de variação da velocidade);
- Utilizar uma pequena bomba auxiliar de aumento de pressão (booster). As necessidades energéticas do sistema global podem ser reduzidas através do uso de uma bomba auxiliar que garanta um escoamento de alta pressão para um determinado utilizador e que permita ao resto do sistema funcionar a uma pressão mais baixa e a uma potência reduzida;
- Limpar ou modificar o diâmetro dos impulsores. Para corrigir o sobredimensionamento de bombas, a carga na sucção pode ser reduzida 10 a 50% através da limpeza ou alteração do diâmetro do impulsor da bomba segundo as recomendações indicadas pelo fabricante;
- Repor as folgas internas. A capacidade e o rendimento da bomba diminuem à medida que as fugas internas aumentam devido a folgas excessivas entre componentes desgastados da bomba;
- Aplicar revestimentos na bomba. A aplicação de revestimentos na bomba reduzirá as perdas por atrito.
Por outro lado os principais problemas associados ao controlo de sistemas de bombagem e respetivas medidas a implementar para solucionar esses problemas podem ser sintetizadas nos pontos seguintes:
- Bombas com grandes variações de caudal ou pressão. Quando os escoamentos ou pressões normais são menores que 75% dos seus valores máximos, está a ser desperdiçada energia. Este desperdício energético devese normalmente a um estrangulamento excessivo, a grandes caudais de desvio (by-pass) ou ao funcionamento de bombas desnecessárias;
- O desvio de caudal por by-pass, quer através de sistemas de controlo ou de orifícios de proteção de perdas de pressão, constitui um desperdício de energia;
- Nos sistemas com múltiplas bombas, a energia é habitualmente desperdiçada por by-pass do caudal em excesso, operação de bombas desnecessárias, excesso de pressão, ou por existir um grande aumento de caudal entre bombas;
- Desligar bombas desnecessárias. Esta medida pode ser realizada após uma redução significativa das necessidades da instalação a alimentar;
- Utilizar variadores eletrónicos de velocidade nos motores elétricos das eletrobombas. Utilizar várias bombas em paralelo para funcionamento de acordo com as necessidades. A utilização de várias bombas em paralelo oferece uma alternativa ao controlo por by-pass, ao controlo por estrangulamento ou aos VEV. Quando os sistemas com múltiplas bombas funcionam a baixo caudal, esta medida aumenta a economia energética porque permite desligar uma ou mais bombas enquanto as restantes funcionam com um rendimento elevado;
- Instalar contadores volumétricos e elétricos para monitorizar o desempenho do sistema. Deve ser feito um registo regular dos indicadores de desempenho do sistema. Este registo regular deve acompanhar adequadamente o funcionamento do sistema e, se necessário, deve ser usado como informação de base para futuras melhorias no controlo.
A eficiência total de um sistema de bombagem depende da eficiência dos vários componentes do sistema. Como se pode ver no exemplo da Figura 3.5, para a mesma potência de saída, o sistema ineficiente absorve mais do dobro da potência absorvida pelo sistema otimizado, realçando a importância do design de sistemas motorizados integrados 24.
![Figura 3.5 – Comparação de um sistema de bombagem convencional com um sistema de bombagem de alta eficiência possuindo um VEV. Ambos os sistemas debitam a mesma potência de saída [24]](/sites/default/files/inline-images/figura-3.5.png)
Figura 3.5 – Comparação de um sistema de bombagem convencional com um sistema de bombagem de alta eficiência possuindo um VEV. Ambos os sistemas debitam a mesma potência de saída 24
De acordo com o exemplo da Figura 3.5, duas das principais medidas que transformam sistemas convencionais em sistemas de bombagem de alta eficiência são: aplicação de VEV que permitem variar a velocidade de rotação dos motores elétricos e a substituição de bombas convencionais por bombas mais eficientes.
De referir ainda, que existem grandes diferenças de rendimento hidráulico (eficiência) entre as bombas convencionais e as bombas de alto rendimento. Em alguns casos, esta diferença pode ultrapassar os 10%, como é o caso do exemplo da Figura 3.5, em que esta diferença se situa nos 11%.
A medida que possibilita as maiores oportunidades de economia energética é aquela que através da aplicação de VEV, converte os grupos de eletrobomba de velocidade constante em grupos eletrobomba de velocidade variável. Assim, é dada especial atenção a esta medida na secção seguinte.
3.2.1 Aplicação de VEV aos Sistemas de Bombagem
Em alguns sistemas de bombagem podem ser alcançadas reduções no consumo de energia elétrica que dependem do caudal relativo e em certos casos podem situar-se acima de 65% simplesmente com a aplicação de variadores eletrónicos de velocidade nos motores elétricos das eletrobombas. Tendo em conta que atualmente cerca de 80% das eletrobombas aplicadas em todo o mundo são unidades de velocidade constante, o potencial de economia de energia desta medida tem um valor extremamente elevado.
A Figura 3.6 apresenta a variação de potência elétrica necessária para controlar o caudal de uma bomba. Usando uma válvula convencional (controlo por estrangulamento), verifica-se que reduzindo o caudal, a potência absorvida pouco decresce. Se, pelo contrário, a redução do caudal é conseguida através da redução de velocidade da bomba, então a potência absorvida decresce fortemente. Assim, a Figura 3.6 apresenta, de forma gráfica, a economia energética potencial decorrente da aplicação do controlo de velocidade através de um VEV.
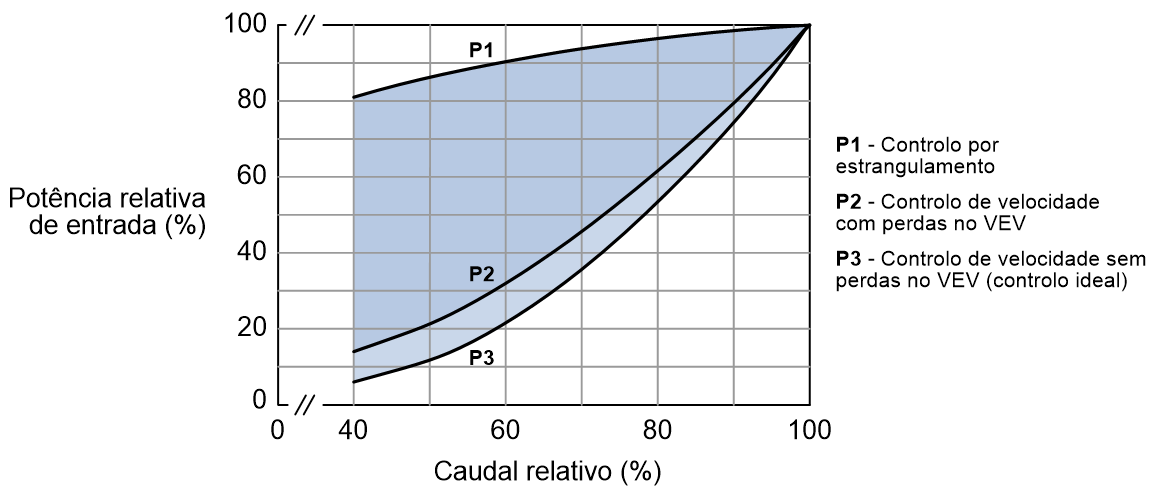
Figura 3.6 – Potência relativa de entrada para vários métodos de controlo do caudal de uma bomba centrífuga
É ainda de salientar que, no caso das bombas, existe uma relação do tipo aproximadamente cúbico entre a velocidade de rotação e a potência mecânica absorvida, enquanto o caudal é aproximadamente proporcional à velocidade de rotação. Destas relações, infere-se que reduzindo, por exemplo, o caudal em 20%, o consumo de energia elétrica pode ser reduzido para metade.
A Figura 3.7 também permite visualizar a comparação entre regimes de regulação de caudal por estrangulamento e por velocidade regulável da bomba.
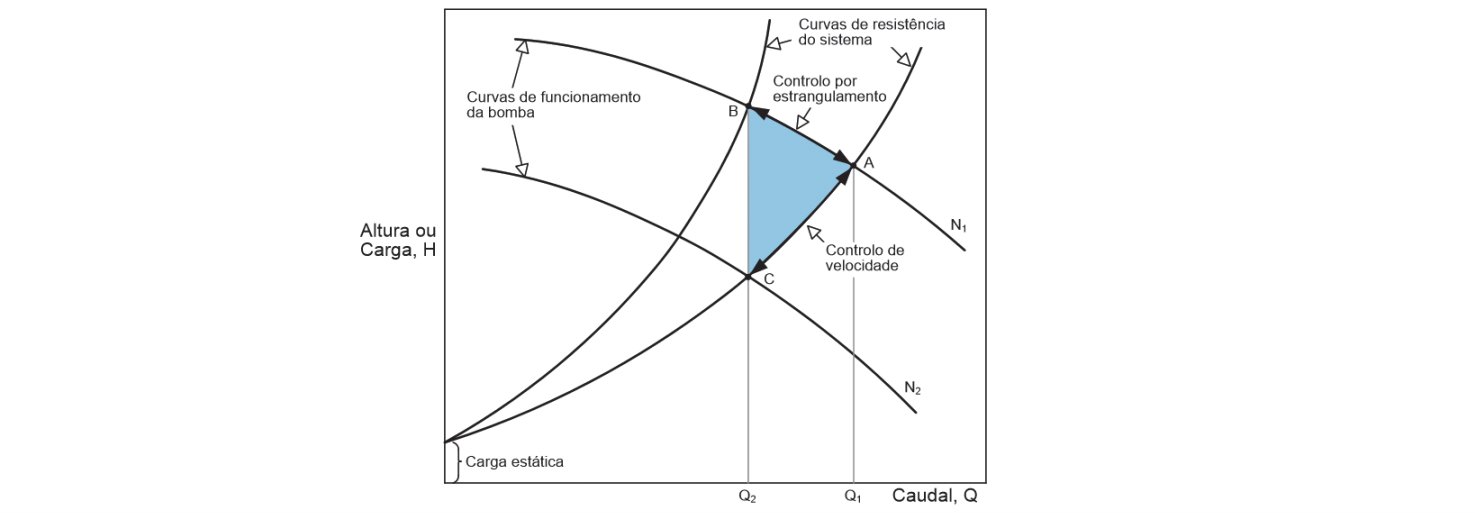
Figura 3.7 – Comparação entre o controlo de caudal por estrangulamento e o controlo de caudal por variação da velocidade de rotação da bomba (através de um VEV)
A gama referida de variação de caudal situa-se entre Q1 e Q2. Para uma velocidade constante da bomba, N1, a válvula de estrangulamento fará deslocar o ponto de funcionamento entre A e B. Se a velocidade variar entre N1 e N2, o ponto de funcionamento deslocar-se-á entre A e C para as mesmas variações de caudal. Não só esta linha corresponde a um conjunto de pontos de maior rendimento como também corresponde a produtos menores de H por Q e, portanto, a um menor consumo de energia.
Refira-se ainda que em muitas aplicações de bombagem, onde são utilizadas várias bombas em paralelo para produzir o caudal requerido, a substituição do tradicional ciclo on/off pela operação contínua de todas as bombas com velocidade variável (através da utilização de VEV) leva a economias de energia elétrica significativas 24. Esta situação exemplificada na Figura 3.8 é especialmente indicada para sistemas onde a altura manométrica a vencer não é um fator importante.
Outras vantagens da operação contínua com variação de velocidade são 24:
- Eliminação dos arranques bruscos típicos dos ciclos on/off;
- Controlo do efeito de “golpe de aríete” que degrada as tubagens, através de acelerações e desacelerações controladas.
![Figura 3.8 – Dois modos de operação em que as mesmas bombas em paralelo debitam um caudal total igual. Caso A: bombas a operarem em ciclos on/off; e caso B: bombas com variação de velocidade (VEV acoplado) [24]](/sites/default/files/inline-images/figura-3.8.png)
Figura 3.8 – Dois modos de operação em que as mesmas bombas em paralelo debitam um caudal total igual. Caso A: bombas a operarem em ciclos on/off; e caso B: bombas com variação de velocidade (VEV acoplado) 24
3.3 Sistemas de Ventilação
A principal função de um ventilador é movimentar grandes volumes de ar ou gases a pressões que sejam suficientes para superar a resistência dos sistemas aos quais estão agregados. Para reduzir a energia utilizada em ventiladores é necessário ter uma compreensão básica de como os sistemas de ventilação funcionam.
Os principais fatores e considerações a ter em conta para garantir que um sistema de ventilação é eficiente em termos de desempenho e consumo de energia são:
- Selecionar o tipo adequado de motor para o ventilador;
- Determinar a velocidade do ar como parte do projeto de dimensionamento;
- Minimizar a perda de pressão através da tubagem de distribuição;
- Selecionar o ventilador mais adequado para a aplicação particular em questão;
- Efetuar uma instalação correta;
- Efetuar manutenção regular:
- Efetuar uma revisão anual.
No que concerne aos motores elétricos dos ventiladores devem ser aplicadas as mesmas medidas de economia energética já referidas na secção 3.1.
Tal como nos sistemas de bombagem, a instalação de VEV em sistemas de ventilação é a medida que, à partida, conduz a maiores economias energéticas (mesmo em motores já a operar perto da sua carga ótima). Nos sistemas convencionais a energia gasta é elevada sempre que se utilizam válvulas ou dispositivos similares para regular o caudal de ar.
A Figura 3.9 apresenta o exemplo de um chiller onde a instalação de VEV permite controlar a velocidade da bomba e a velocidade do ventilador, com base na emperatura ambiente e na temperatura da saída do fluido refrigerante, respetivamente. O resultado é que comparativamente com a operação baseada em ciclos on/off, este sistema não só permite um controlo mais estável da temperatura do espaço refrigerado como também leva a reduções do consumo de eletricidade que tipicamente atingem os 25-50% 24.
![Figura 3.9 – Exemplo da aplicação de VEV a um sistema de ventilação: chiller com ventiladores e com a bomba de recirculação de fluido refrigerante acoplado a VEV [24]](/sites/default/files/inline-images/figura-3.9.png)
Figura 3.9 – Exemplo da aplicação de VEV a um sistema de ventilação: chiller com ventiladores e com a bomba de recirculação de fluido refrigerante acoplado a VEV 24
3.4 Sistemas de Compressão de Ar
Existem sistemas de compressão de ar, em Portugal, cuja quantidade de ar produzido não é a adequada tendo como consequência o aumento dos custos de manutenção, as paragens de produção, a diminuição da qualidade dos produtos e o aumento do consumo energético. Os principais constituintes de um sistema de produção de ar são: (i) compressores; (ii) secadores; (iii) reservatório de armazenamento de ar comprimido; (iv) rede de distribuição; (v) filtros; (vi) lubrificadores.
Os principais tipos de compressores encontram-se divididos em dois grupos: (i) compressores volumétricos; (ii) compressores dinâmicos.
Nos compressores volumétricos, a compressão do ar é feita com base na redução do gás a comprimir, este é admitido numa ou mais câmaras de compressão, nas quais o seu volume será reduzido, provocando um aumento da pressão do próprio gás 27. Dentro dos compressores volumétricos temos dois tipos: (i) rotativo – espiral, palhetas, anel líquido, parafuso, roots e dente; (ii) alternativo – pistão de efeito simples, pistão de efeito duplo e diafragma.
No que diz respeito aos compressores dinâmicos, a compressão do gás é efetuada através da conversão de energia cinética em pressão. A massa é acelerada a uma velocidade elevada por meio de um impulsor, posteriormente é forçada a desacelerar ao ser expandida num difusor. O fenómeno de expansão permite a conversão de energia cinética em pressão 27. Os compressores centrífugos e axiais, são exemplos de compressores dinâmicos.
Na Tabela 3.3 encontram-se enumerados os tipos de compressores que estão disponíveis no mercado, bem como algumas condições de operação e as respetivas aplicações.
O ar comprimido é uma forma versátil, flexível e segura de transmitir energia. De facto, mais de 10 % da energia elétrica consumida na indústria é utilizada em ar comprimido. Contudo, perto de 20% desta energia é perdida devido a fugas de ar, má utilização do ar comprimido ou à negligência da manutenção.
Tabela 3.3 – Tecnologia e aplicações de compressores 27

A otimização energética dos sistemas de ar comprimido deverá passar por intervenções nas seguintes áreas: produção e tratamento do ar comprimido; redes de distribuição de ar comprimido; dispositivos de utilização final; projetos e operação do sistema global.
Em termos mais específicos e relativamente às três primeiras áreas, as principais medidas a considerar com vista ao aumento da eficiência dos sistemas de ar comprimido são as apresentadas em seguida.
Produção de ar comprimido
- Otimização da utilização do sistema: ajuste dos controlos e regulação da pressão, desligar quando não utilizado;
- Otimização do nível de pressão do ar comprimido do sistema em função dos dispositivos de utilização final;
- Redução da temperatura do ar de admissão, mantendo uma ótima filtragem na tomada de ar;
- Melhoramento do sistema de controlo do compressor;
- Otimização das mudanças de filtros (em função da queda de pressão);
- Filtração e secagem do ar até aos requisitos mínimos do sistema (possivelmente mediante instalação de filtros/ secadores pontuais para necessidades específicas);
- Recuperação e utilização do calor desperdiçado através dos sistemas de arrefecimento dos compressores;
- Aumento da capacidade do reservatório principal de ar comprimido;
- Utilização de variadores eletrónicos de velocidade;
- Utilização de um sistema de múltiplas pressões, com a utilização de boosters para aumentar a pressão em determinados locais;
- Substituição dos motores elétricos convencionais avariados ou em fim de vida por motores de alto rendimento;
- Substituição de compressores exageradamente sobredimensionados por outros com menores consumos específicos de energia e ajustados às necessidades do sistema.
Rede de distribuição de ar comprimido
- Instituição de um programa regular para a verificação de fugas de ar comprimido;
- Redução de fugas com a utilização de adaptadores de fugas reduzidas, uniões rápidas de elevada qualidade, etc.;
- Divisão do sistema em zonas, com reguladores de pressão apropriados ou válvulas de corte;
- Fecho de linhas que estão fora de serviço;
- Utilização de purgas de condensados do tipo “sem perdas de ar”;
- Dimensionamento adequado das capacidades de armazenamento (permite que os compressores funcionem com um rendimento otimizado e evita arranques e paragens bruscas);
- Instalação de reservatórios suplementares de ar comprimido próximos de cargas variáveis;
- Diminuição da extensão da rede e criação de uma rede em anel;
- Otimização do diâmetro da tubagem;
- Limitação do número de cotovelos, de mudanças de direção e de mudanças de seção.
Dispositivos de utilização final
- Eliminação de utilizações não apropriadas de ar comprimido;
- Reparação ou substituição de equipamentos com fugas de ar comprimido;
- Interrupção do ar comprimido quando o dispositivo não está em operação;
- Verificação e otimização da necessidade de dispositivos específicos de regulação de pressão, filtros e secadores;
- Utilização preferencial de aspiradores elétricos nas limpezas. Estes consomem menos energia que os aparelhos insufladores de ar (bicos de sopro ou pistolas de ar).
A avaliação de cada uma das medidas acabadas de referenciar deve ter em conta a respetiva aplicabilidade e rentabilidade, tendo em conta não apenas o custo do investimento necessário e as economias de energia anuais, mas também outras eventuais alterações nos custos anuais de operação e manutenção dos sistemas de ar comprimido em questão.
De todas as medidas referenciadas anteriormente, as mais importantes são: redução de fugas de ar comprimido; melhor conceção do sistema; utilização de variadores eletrónicos de velocidade; recuperação de calor.
A Tabela 3.4 resume a contribuição potencial, em termos de economias energéticas, de algumas das principais medidas técnicas referenciadas 28:
Tabela 3.4 – Valores típicos de economia de energia associados a várias medidas 28
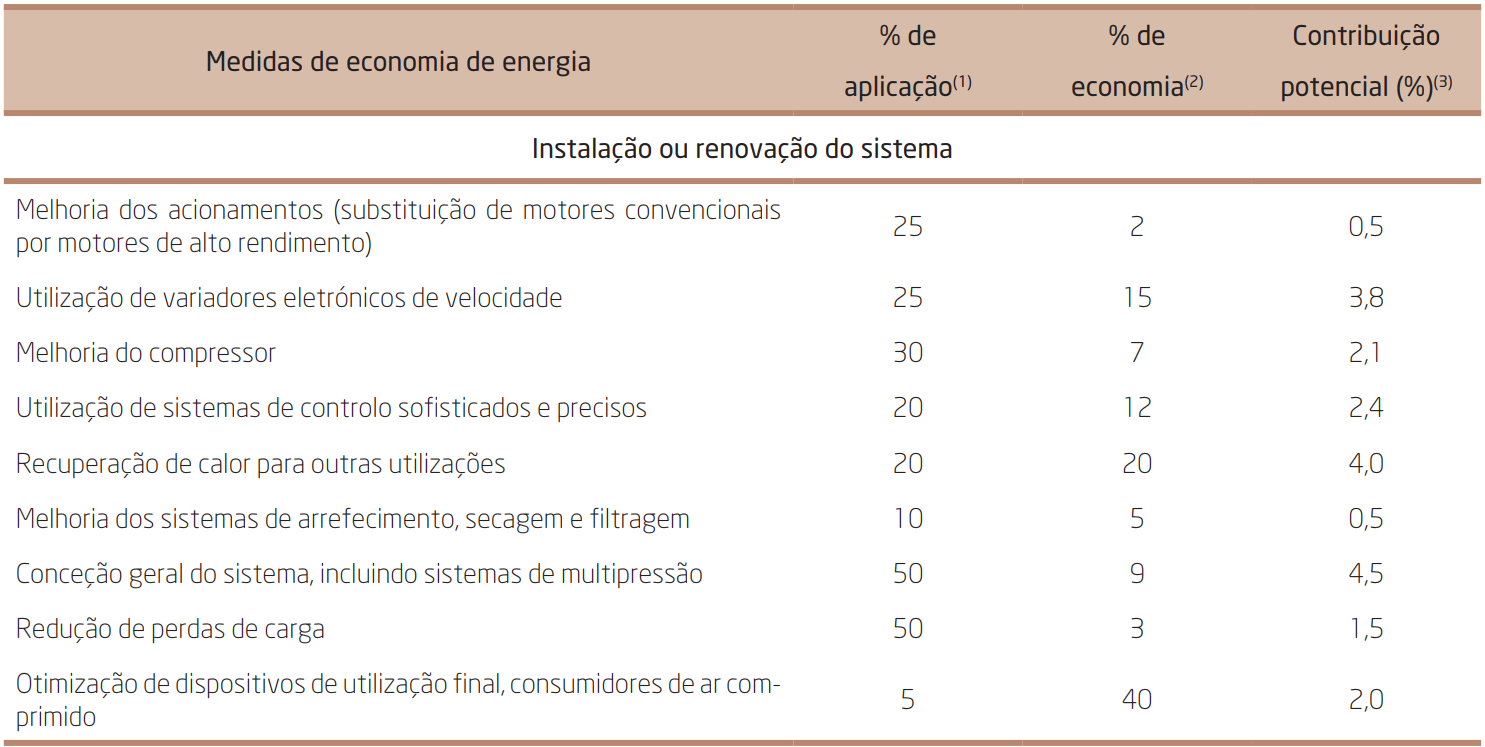
A redução do consumo de eletricidade é mais facilmente conseguida a partir de uma correta conceção dos sistemas e, portanto, aquando da instalação de um sistema novo. No entanto, também são possíveis economias significativas aquando da substituição dos principais componentes de um sistema já existente. Além disso, ações relacionadas com a operação e manutenção, nomeadamente a manutenção regular de filtros e a deteção de fugas de ar comprimido, podem ser introduzidas em qualquer momento do ciclo de vida de um sistema de ar comprimido 28.
Em seguida são abordados, em maior detalhe, algumas medidas e/ou soluções tecnológicas referenciadas anteriormente, cuja aplicação em sistemas de ar comprimido pode levar a reduções energéticas consideráveis.
3.4.1 Otimização da Pressão do Ar Comprimido
Na indústria é prática corrente produzir ar comprimido a pressão elevada e depois expandi-lo até à pressão desejada, com grandes perdas neste procedimento. A solução mais energeticamente favorável é a produção de ar comprimido à pressão mínima requerida (p. ex., redução de pressão do compressor de 8,2 bar para 6,9 bar permite ganhos energéticos de 9,1% na potência de compressão).
Como regra de base, pode afirmar-se que para uma redução de 1 bar na pressão de trabalho da rede, a redução de energia elétrica associada pode atingir os 6%. Estas economias energéticas são conseguidas com a ajuda de sistemas de controlo apropriados.
A utilização de controladores baseados em computadores industriais é frequente em sistemas modernos de produção e tratamento de ar comprimido. Estes sistemas podem ser utilizados apenas no controlo do compressor ou no controlo global dum sistema completo de ar comprimido. Com tais sistemas de controlo, a pressão máxima de trabalho pode ser reduzida, as perdas de potência são significativamente reduzidas e é conseguido um controlo efetivo dos custos.
A simples redução da pressão do sistema através de controladores modernos também tem outra vantagem: a diminuição das perdas causadas por fugas no sistema de distribuição do ar comprimido, sem que tal esteja associado a qualquer reparação.
3.4.2 Utilização de Variadores Eletrónicos de Velocidade
O funcionamento em modo carga-vazio não tira partido da operação em modo contínuo dos compressores. O uso de VEV ajusta a velocidade do compressor em função das exigências do sistema, permitindo inclusive desligar o compressor quando este não está a ser utilizado.
A integração de VEV em sistemas de ar comprimido pode revelar-se bastante viável do ponto de vista económico em situações de carga variável, o que acontece em cerca de um quarto das instalações existentes. Ainda assim, a utilização de VEV limita-se à instalação de novos compressores, já que a reconversão de compressores já instalados coloca normalmente vários problemas técnicos 28.
Entre as vantagens da utilização de VEV encontram-se 25:
- Redução de fugas, diminuindo as oscilações bruscas de pressão associadas ao modo de funcionamento em carga-vazio;
- Maior durabilidade do compressor.
3.4.3 Melhoramentos do Sistema de Controlo de Funcionamento Carga/Vazio
No sistema de controlo de funcionamento em carga/vazio, um compressor pode estar bastante tempo em vazio, estando em funcionamento sem gerar pressão útil para o sistema. Há que ter presente que um compressor a funcionar em vazio, embora dependendo do tipo de compressor e do sistema de acionamento, poderá consumir cerca de 20% da energia a plena carga. Nestes casos, a otimização passa pela utilização de compressores pouco sobredimensionados, ou por uma série de compressores de menores dimensões de modo a que seja possível desligar alguns quando as necessidades do sistema são menores.
3.4.4 Redução de Fugas de Ar Comprimido
De todas as medidas que levam a economias energéticas, a redução de fugas de ar comprimido é a medida mais importante, sendo aplicável a quase todos os sistemas de ar comprimido. A maior parte dos utilizadores de ar comprimido é pouco sensível à importância de um programa regular de deteção de fugas, em parte porque são invisíveis e geralmente não provocam danos.
Uma rede de distribuição concebida e instalada corretamente pode diminuir significativamente as fugas de ar comprimido, por exemplo, através da utilização de dispositivos modernos de drenagem de condensados sem perdas de ar, ou através da especificação de ligações de elevada qualidade e duração. Contudo, o aspeto essencial relacionado com este tópico tem a ver com uma manutenção adequada. Existem no mercado aparelhos de uso manual que detetam as fugas de ar comprimido
pelo ruído que estas provocam, permitindo a redução dos custos associados à deteção de fugas.
3.4.5 Recuperação e Utilização do Calor Desperdiçado pelos Compressores
Em operação, os compressores geram calor que tanto quanto possível deverá ser recuperado e utilizado noutras aplicações. Uma vez conhecidos os sistemas de recuperação de calor e a disponibilidade do calor gerado na compressão, o potencial de recuperação desta energia térmica e a escolha do sistema de recuperação dependem dos seguintes fatores 25:
- Tipo de compressor: blindado ou não, alternativo ou de parafuso, volumétrico ou dinâmico;
- Tipo, caudal e temperatura do fluido de arrefecimento do compressor (água, ar ou óleo);
- Existência, a curta distância e no mesmo instante, de áreas a aquecer, caldeiras ou outros equipamentos consumidores de energia térmica;
- Tempo de funcionamento e fator de carga do compressor.
Os sistemas de recuperação de calor baseiam-se essencialmente no aquecimento de ambientes próximos, através de condutas de ar quente e, eventualmente, recorrendo a ventiladores de baixa pressão para compensar o aumento das perdas de carga adicionais introduzidas pelas condutas. As vantagens destas instalações residem na sua simplicidade e baixo custo, mas não permitem a acumulação da energia recuperada e têm caráter sazonal 28.
A recuperação de calor produzido pelos compressores é uma operação cuja viabilidade económica depende do custo e disponibilidade do equipamento necessário (permutadores de calor, tubagem, reguladores, etc.) e da comparação com soluções alternativas.
3.4.6 Discussão sobre Configuração de Compressores – Um Exemplo
Pretende-se efetuar a compressão de 100 m3/h de ar a 25 °C, de 1 atm para 15 atm. Qual a melhor estratégia para atingir este objetivo?
Esta compressão deverá utilizar um compressor de múltiplos andares, visto que é bem aceite que o rácio de compressão máximo não deve ultrapassar o valor 3. Foram, efetuadas simulações recorrendo ao pacote de simulação AspenPlus de modo a verificar o impacto que o rácio de compressão tem na potência do compressor.
Foram simulados três casos. O primeiro consiste num compressor de 3 andares, em que nos dois primeiros o rácio de compressão é 3 e no último esse valor é de 1,67 para perfazer as 15 atm. Entre cada andar encontra-se um arrefecedor, pois a corrente de ar que sai de um compressor com destino ao compressor seguinte, não pode exceder os 215 °C. O segundo e o terceiro caso, diferem do primeiro, no valor da temperatura de saída de cada um dos arrefecedores.
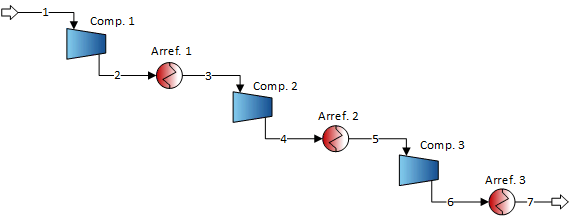
Figura 3.10 – Esquema de compressão em 3 andares com arrefecimento intermédio para o exemplo apresentado
Os resultados obtidos para os valores das principais variáveis encontram-se apresentados na Tabela 3.5.
Tabela 3.5 – Resultados da simulação do Caso 1
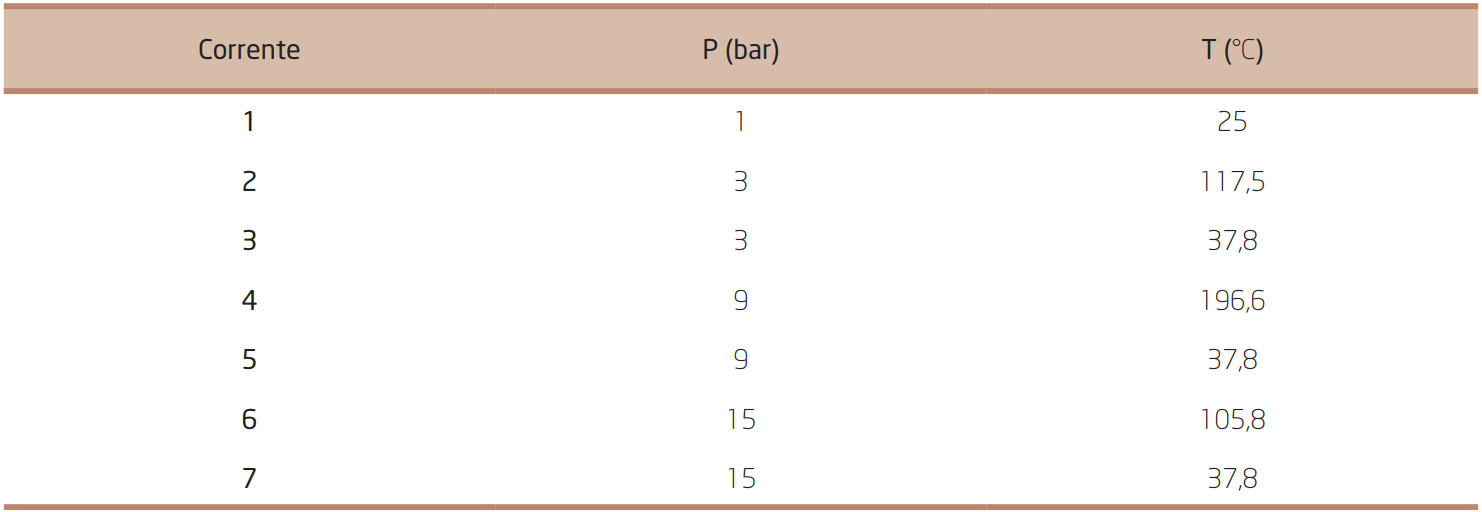
Como é possível verificar, a temperatura não excede em nenhum dos compressores, o valor de 210 °C, pelo que nesta simulação os valores de temperatura e pressão estão dentro da gama recomendada segundo as boas práticas industriais.
Outras simulações, considerando a configuração base dos três compressores e as respetivas razões de compressão, mostram a influência do arrefecimento do ar à saída do compressor na potência consumida pelos compressores seguintes. Nesta análise, estudou-se o efeito do arrefecimento a 50 °C ou a 75 °C.
Os resultados da simulação mostram (Tabela 3.6), como seria de esperar, que o consumo de água aumenta com o grau de arrefecimento nos estágios intermédios, enquanto a potência consumida pelo compressor diminui para valores mais baixos de temperatura de ar no arrefecimento. Em conclusão, a minimização dos custos globais do sistema de compressores, deve ser um tradeoff entre o consumo de água de refrigeração e o consumo de eletricidade, sendo que o valor ótimo da temperatura de saída do ar vai depender dos custos de ambas as utilidades.
Tabela 3.6 – Resultados obtidos alterando as condições de arrefecimento do ar
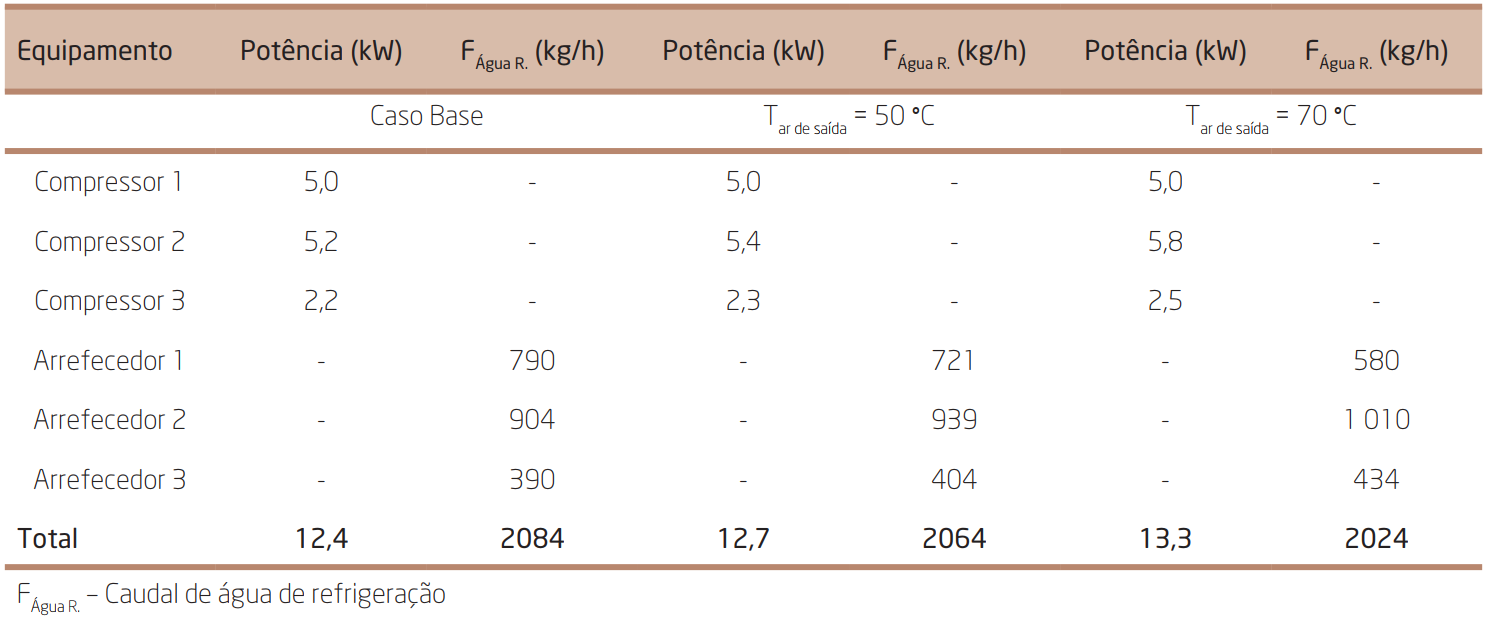
3.5 Sistemas de Transportadores de Sólidos
Os custos de transporte de sólidos podem representar uma parcela muito relevante nos custos operatórios de uma unidade industrial.
Na indústria, o transporte de materiais sólidos pode ocorrer pela movimentação desses sólidos fluidizados (transporte pneumático) ou, quando o material apresenta granulometria grosseira ou é abrasivo, através de dispositivos mecânicos que transportam os sólidos em regime contínuo. A escolha do tipo de transportador está fortemente dependente da função que irá desempenhar, tal como se apresenta na Tabela 3.7.
Os equipamentos podem dividir-se em dois grandes grupos:
- Móveis, que se movimentam ao mesmo tempo que o material que transportam (guindastes, empilhadoras);
- Fixo, cuja posição permanece fixa durante o tempo, embora possam conter partes móveis (pneumáticos, elevadores de cestos, arrastadores).
Tabela 3.7 – Transportador para material a granel 29
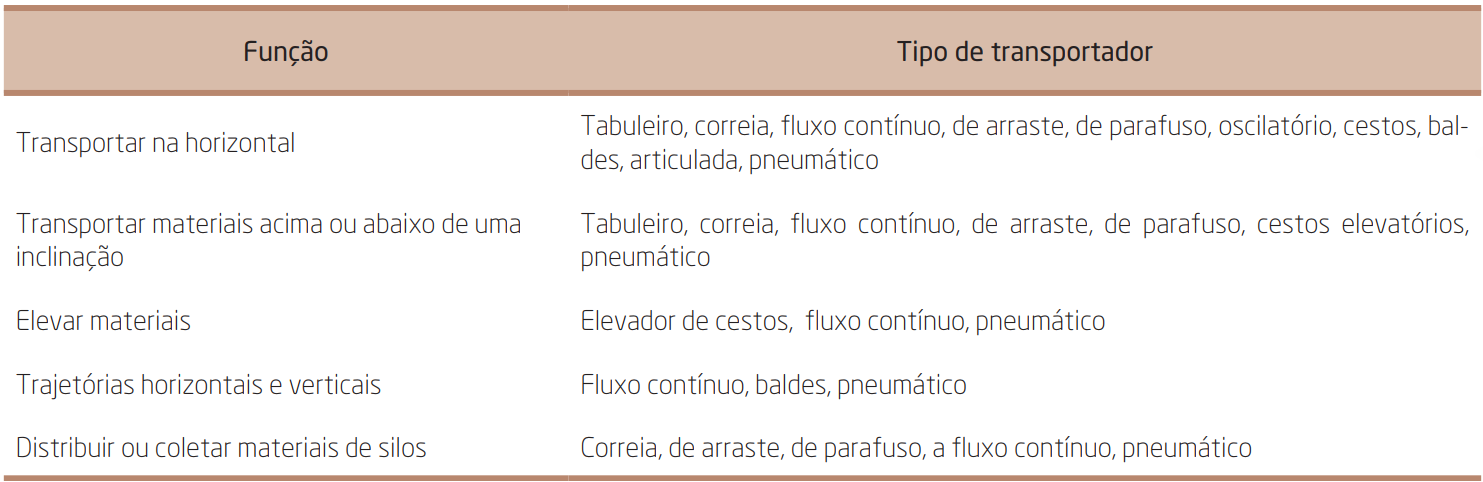
Na indústria, a seleção e o dimensionamento do equipamento a ser utilizado dependem de muitos fatores, sendo os mais importantes:
- A capacidade, diretamente relacionada com a quantidade de material processado e armazenado na unidade;
- A distância e o desnível entre carga e descarga que influenciam diretamente a construção do equipamento de transporte;
- A natureza do material a ser transportado, uma vez que permanece muitas vezes em contato direto com o transportador. A granulometria, a forma da partícula, a densidade, a fragilidade, a humidade, a dureza e a aglomeração podem ser características determinantes na escolha do equipamento;
- Os fatores económicos que influenciam a qualidade e tipo de equipamento.
- Apresenta-se em seguida a descrição das tecnologias de transporte de sólidos existentes atualmente.
3.5.1 Transportadores de Correias
Os transportadores de correia são muito utilizados para o transporte de materiais sólidos dentro da indústria devido ao seu baixo custo, construção compacta e excelente desempenho funcional. São compostos por uma correia sem fim que trabalha sob o efeito da força de atrito.
Estes sistemas podem ser horizontais ou inclinados e de comprimentos variados. Operam a uma velocidade de até 5 m/s e transportam, no máximo, 5 ton/h. Podem também operar em distâncias curtas, com velocidades baixas, permitindo a manipulação individual dos materiais transportados.
As correias são fabricadas numa grande variedade de materiais, como couro, nylon, poliéster, polietileno, PVC, mas normalmente são de borracha com reforço de fios metálicos. A espessura e o material a ser utilizado depende do tipo de material a ser transportado, da largura e da tensão aplicada.
A Figura 3.11 representa esquematicamente um transportador por correia
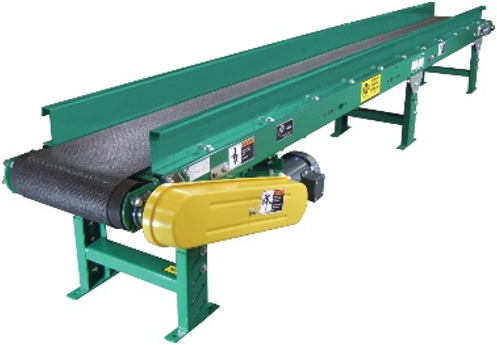
Figura 3.11– Exemplo de um sistema de transporte de sólidos por correias 30
3.5.2 Transportadores de Esteiras
Este tipo de sistema é uma variação do transportador de correia aplicável ao transporte pesado de materiais quentes ou muito abrasivos, ou ainda quando se deseja percursos diferentes. A esteira é geralmente metálica e construída com bandejas ou caçambas fixas numa correia ou corrente.
Muitas vezes as esteiras são reforçadas para atender à necessidade de transporte de pesados a curtas distâncias.
A esteira transportadora pode ter secções diferentes, em função da disposição dos rolos, que são escolhidos com base no material a ser transportado.
3.5.3 Transportadores por Gravidade
O Transportador por gravidade é considerado o sistema mais simples para o transporte de sólidos. É utilizado em processos onde a relação custo-benefício não justifica a colocação de um motor para o acionar. São implementados devido à natureza do processo. O sólido escoa por gravidade sobre um plano inclinado em relação à horizontal com um ângulo superior ao do repouso do material. O transportador por gravidade pode ser em roldanas ou dutos inclinados por onde o sólido escoa livremente. O ângulo de inclinação determinará a velocidade do escoamento das partículas. Quanto maior o ângulo de inclinação, mais as partículas vão ser aceleradas durante o processo de transporte podendo haver queda excessiva das partículas.
3.5.4 Transportadores de Rosca/Parafuso (helicoidal)
Os transportadores de rosca consistem num tubo ou calha em forma de U pela qual um parafuso sem fim, com ou sem eixo central, gira pela ação de um motor. É adequado ao transporte de materiais granulares, densos ou volumosos e viscosos. É um dos principais modos de alimentação de sólidos em secadores ou incineradores.
Na Figura 3.12 encontra-se representado uma ilustração deste tipo de transporte.
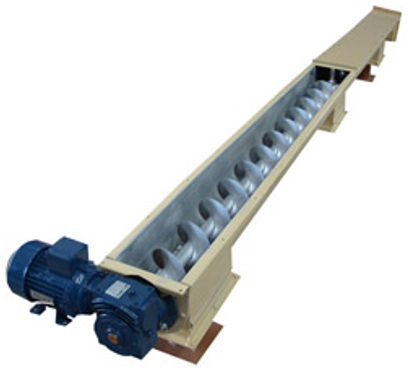
Figura 3.12 – Representação de um sistema de transporte helicoidal de calha 31
3.5.5 Transportador Vibratório
Os transportadores vibratórios são constituídos por um tabuleiro horizontal suportado por molas e posto a vibrar através de um braço. O movimento para cima e para a frente incutido às partículas, dá-lhes movimento através de uma sequência de pequenos saltos.
3.5.6 Transportador Pneumático
O transporte pneumático consiste em movimentar um produto sólido no interior de uma tubagem através de uma corrente com ar ou outro gás como fluido transportador.
O transportador pneumático é um equipamento utilizado em larga escala na indústria para movimentação e elevação de sólidos através das mais variadas distâncias e tipos de trajeto.
O sistema de transporte pneumático é constituído basicamente por:
- Tubulação por onde circulam os sólidos e o fluido transportado;
- Um ventilador e/ou bomba de vácuo; ➢ Um alimentador de sólidos;
- Um separador de fluido e sólido na parte terminal tais como:
- Ciclones;
- Filtros de limpeza por ar comprimido ou contra-corrente.
Este tipo de sistema é útil para transportar sólidos para locais de uma zona do processo, difíceis ou economicamente inviáveis de serem transportados por transportadores mecânicos, e apresenta como vantagens: (i) um consumo eficiente de energia e mão-de-obra; (ii) um menor desgaste do sistema; (iii) uma maior flexibilidade, permitindo instalações de sistemas complexos em espaços bem reduzidos.
As desvantagens destes transportadores são: (i) elevado custo de instalação; (ii) baixa viabilidade para curtas distâncias; (iii) limitação da distância no transporte de materiais frágeis; (iv) exigência de um gás inerte no transporte de materiais potencialmente explosivos.
3.5.7 Transportador de Elevador de Cestos
Estes transportadores são sistemas constituídos por cestos fixos sobre correias verticais ou de grande inclinação. Movimentam-se geralmente no interior de caixas de madeiras ou de aço. A descarga é feita pela inversão dos cestos.
São utilizados para a elevação de cereais, carvão, minérios e reagentes químicos a granel. A altura de elevação pode chegar a 100 m.
- 20 ADENE, “Cursos de utilização Racional de Energia - Eficiência Energética na Indústria”, Gaia, 2004.
- 21 EDP, “Soluções de Eficiência PME - Motores de Alto Rendimento”.
- 22 A. ISR-UCoimbra, “Guia Técnico - Soluções para melhorar os sistemas acionados por motores elétricos,” 2007.
- 23 Comissão Europeia/CEMEP, “Electric motor efficiency - Saving Europe’s energy and environment”, 2003.
- 24 A. T. de Almeida, F. J. T. E. Ferreira e D. Bock, “Technical and Economical Considerations in the Application of Variable-Speed Drives With Electric Motor Systems”, IEEE Transactions on Industry Applications, vol. 41, pp. 188-199, 2005.
- 25 European Commission, “Reference Document on Best Available Techniques for Energy Efficiency”, Fevereiro 2009.
- 26 ADENE, “Medidas de Eficiência - Indústria”
- 27 ADENE, “Manual de Eficiência Energética em Sistemas de Ar Comprimido”, 2016.
- 28 P. Radgen e E. Blaustein, “Compressed Air Systems in the European Union – Energy, Emissions, Savings Potential and Policy Actions”, 2001.
- 29 H. Feise, “Chemical Engineering and Chemical Process Technology - Handling of Solids”, vol. II, UNESCO-EOlSS, 2010.
- 30 ACSI
- 31 BraNorte