Capítulo 6
Recuperação de Calor
A recuperação de calor é uma das ferramentas no âmbito da engenharia de processos que permite uma redução significativa no consumo de energia no setor industrial. A recuperação de calor tem como principal objetivo aproveitar, da melhor forma possível, o excesso de calor das correntes do processo que tenham um nível térmico superior ao que é requerido para ser usado em zonas deficitárias.
A recuperação do excesso de calor pode ser obtida a partir de várias fontes:
- Gases de combustão;
- Efluentes quentes ou frios;
- Ar de exaustão;
- Água de arrefecimento e óleo hidráulico;
- Calor de sobreaquecimento e de condensação rejeitados dos processos de refrigeração;
- Correntes do processo que necessitem de ser arrefecidas.
As tecnologias mais comuns para o aproveitamento deste calor são:
- Uso direto, por exemplo, dos gases de combustão nos permutadores de calor;
- Utilização de bombas de calor e recompressão de vapor, que transformam o calor de modo a gerar energia mais útil ao processo promovendo o aumento da temperatura inicial;
- Recurso a operações multi-estágio, tais como evaporadores multi-efeito, expansão de vapor e combinações das técnicas acima mencionadas.
Metodologias de Integração de Processos podem ser utilizadas para uma melhor identificação dos potenciais energéticos existentes no conjunto do processo, encontrando a melhor configuração possível para a permuta entre correntes e as melhores condições de operação do processo que conduzam ao consumo mínimo de energia primária externa.
6.1 Permutadores de Calor
Um permutador de calor permite a recuperação direta de calor, ou seja a transferência de calor entre dois fluidos através de uma superfície sólida. A transferência de calor ocorre por convecção e condução, fluindo o calor naturalmente das temperaturas mais elevadas (fonte de calor) para as zonas com temperaturas mais baixas (destino de calor).
A escolha do tipo de permutador e dos diferentes materiais de construção deve ter em atenção a gama de temperaturas de operação e as propriedades físicas dos fluidos envolvidos na transferência de calor.
Devido ao seu design, os permutadores de caixa e tubos com pitch triangular que utilizem vapor flash impuro do lado da caixa, podem ter graves problemas devido ao depósito de sólidos. Se o vapor arrastar consigo gotículas de líquido e espumas que contenham quantidades apreciáveis de sólidos dissolvidos, estes terão tendência a depositarem-se na superfície exterior dos tubos que se situam perto da entrada de vapor na caixa. Este fenómeno diminui a eficiência energética do permutador, dificulta a sua limpeza, podendo mesmo levar à inutilização deste. uma das soluções poderá ser a alteração para um pitch quadrangular e mais largo.
6.1.1 Manutenção
Devido à sua importância na maioria dos processos industriais, uma manutenção eficaz dos permutadores de calor é imprescindível. Não existindo uma limpeza regular das paredes do permutador, a formação de incrustações e detritos vai diminuir a eficiência da transferência de calor ou dar origem à falha do equipamento.
Para manter a performance dos permutadores de calor recomenda-se 40:
- Aumentar ocasionalmente a velocidade de escoamento;
- Executar uma limpeza com jato de alta pressão;
- Incluir ciclos de limpeza programados;
- Realizar limpezas in situ e profundas “até ao metal”;
- Incluir a limpeza das superfícies externas (casco, espelhos, chicanas, etc.);
- Usar as ferramentas apropriadas de acordo com o tipo de sujidade;
- Não aceitar métodos de limpeza standard.
No caso de estarem sujeitos a uma limpeza rotineira com ácido para renovar a superfície interna dos tubos e recuperar a eficiência do processo de transferência de calor, os permutadores devem ser resistentes ao ácido (construídos geralmente em aço inoxidável), traduzindo-se numa maior durabilidade.
6.2 MetodologIas de Integração de Processos
A Integração de Processos surgiu, na década de 70 como uma área científico-tecnológica devidamente estruturada no âmbito da engenharia de processos, mas trouxe já um elevado impacto à comunidade industrial. os benefícios da sua aplicação em vários setores industriais traduzem-se geralmente em processos mais competitivos económica e ambientalmente 41.
Uma integração significa combinar necessidades/tarefas de tipos opostos para que possam ser obtidas economias ou sinergias. Exemplos desta integração nas indústrias de processo são:
- Integração energética
- Recuperação de calor;
- Refrigeração e condensação integradas com aquecimento e evaporação;
- Projeto da correspondente rede de permutadores de calor.
- Integração de potência
- Expansão integrada com compressão;
- Mesmo eixo ou combinado em compander.
- Integração química
- Subprodutos de uma unidade podem ser utilizados como matéria-prima em outras unidades;
- A ideia de integração de materiais é utilizada em clusters.
- Integração de equipamentos
- Várias operações unitárias (reação, separação, transferência de calor) são integradas na mesma peça de equipamentos, a isto chama-se a intensificação de processos.
O principal foco da Integração de Processos é reduzir significativamente os custos de produção, satisfazendo políticas de utilização racional de energia e de matérias-primas, bem como, a redução de efluentes e subprodutos e a minimização de emissões gasosas. uma das áreas mais importantes da Integração de Processos é efetivamente a integração energética, que pode ser aplicada em projetos novos ou em fábricas que já se encontrem instaladas, tanto em processos simples como nos de elevada complexidade, que operem em contínuo ou em descontínuo. Existem várias metodologias de integração energética que permitem determinar os valores ótimos das variáveis de projeto que minimizem os custos globais do sistema e aproveitem ao máximo o potencial energético do processo: métodos heurísticos, estocásticos, programação matemática, análise exergética, e a Análise do Ponto de Estrangulamento (Pinch Analysis). A metodologia da Análise do Ponto de Estrangulamento é apresentada neste capítulo, através da sua aplicação a um exemplo prático.
6.2.1 Conceitos Básicos da Análise do Ponto de Estrangulamento
As correntes de processo podem requerer aquecimento ou arrefecimento, pelo que se impõe o uso de utilidades. quando se recorre exclusivamente a utilidades externas ao processo, o consumo de energia é maximizado pelo que a respetiva competitividade é prejudicada.
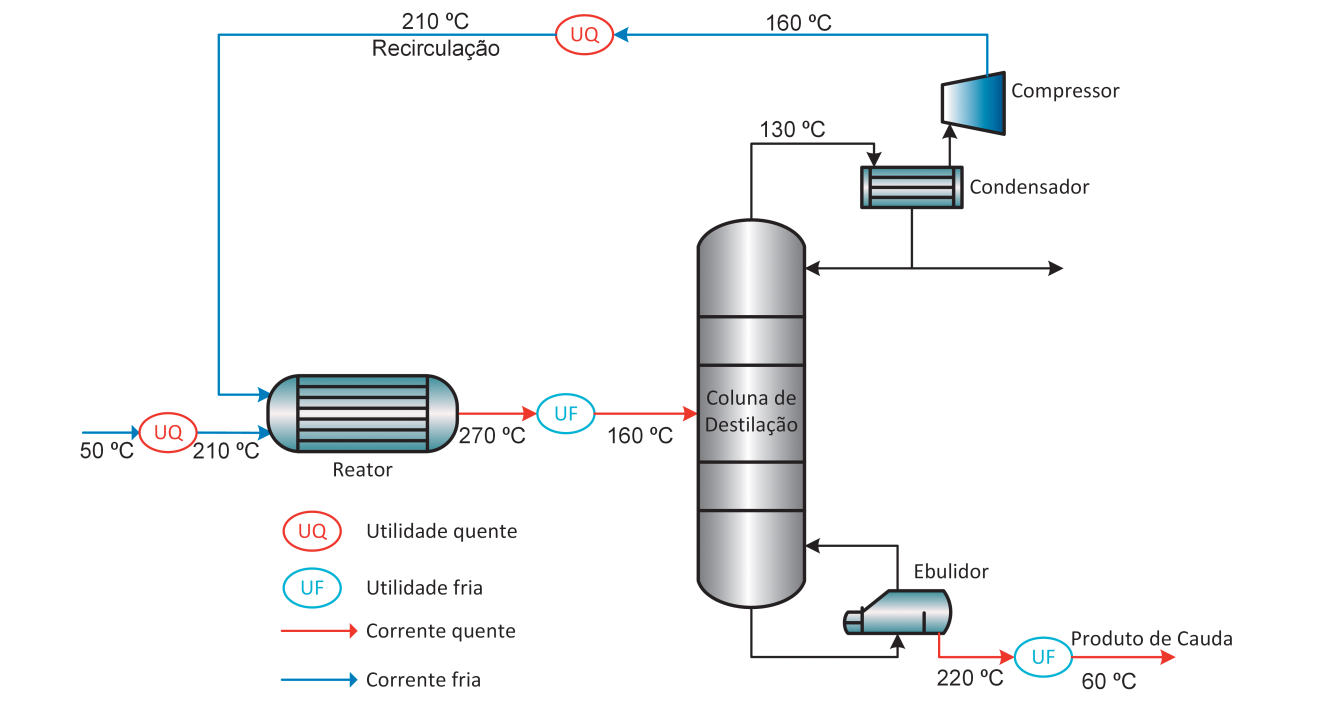
Figura 6.1– Esquema de um processo químico tipo: exemplo de aplicação
A Figura 6.1 apresenta o esquema de um exemplo de aplicação, onde são evidenciadas as correntes que utilizem, neste caso, exclusivamente utilidades exteriores ao processo. Neste esquema identificam-se quatro correntes que necessitam de aquecimento ou de arrefecimento usando utilidades exteriores. Numa primeira abordagem é necessário definir alguns conceitos básicos:
- Correntes frias – Estas correntes recebem calor porque a sua temperatura precisa de aumentar e/ou porque sofrem uma mudança de estado por absorção de calor. Estas necessidades são satisfeitas por um fluido de aquecimento, usualmente vapor de água;
- Correntes quentes – Estas correntes cedem calor porque a sua temperatura precisa de diminuir e/ou porque sofrem uma mudança de estado por libertação de calor. Estas necessidades são satisfeitas por um fluido de arrefecimento, usualmente água de refrigeração;
- Utilidades Externas – fluidos exteriores ao processo que permutam diretamente calor com as correntes, para fornecer ou retirar calor. Podem ser quentes (vapor de água, fluidos térmicos, gases de combustão, entre outros) ou frias (água de refrigeração, ar atmosférico, fluido de arrefecimento, entre outros);
- ∆Tmin – Diferença mínima de temperatura atingida entre duas correntes que trocam calor. Num permutador de calor em contracorrente, os perfis de temperatura das correntes aproximam-se num dos extremos. Esta diferença mínima de temperaturas é estabelecida segundo critérios de projeto e tem influência nos custos de capital do processo. Se for selecionado um valor mais elevado de ∆Tmin, a recuperação de calor no permutador diminui, ainda que com uma menor área de transferência exigida, e a necessidade de utilidades externas aumenta. Assim, a seleção do valor de ∆Tmin tem implicações nos custos de capital e de energia. valores típicos de ∆Tmin baseados na experiência estão disponíveis na literatura para referência e são listados na tabela seguinte.
Tabela 6.1 – Valores de ΔTmin típicos
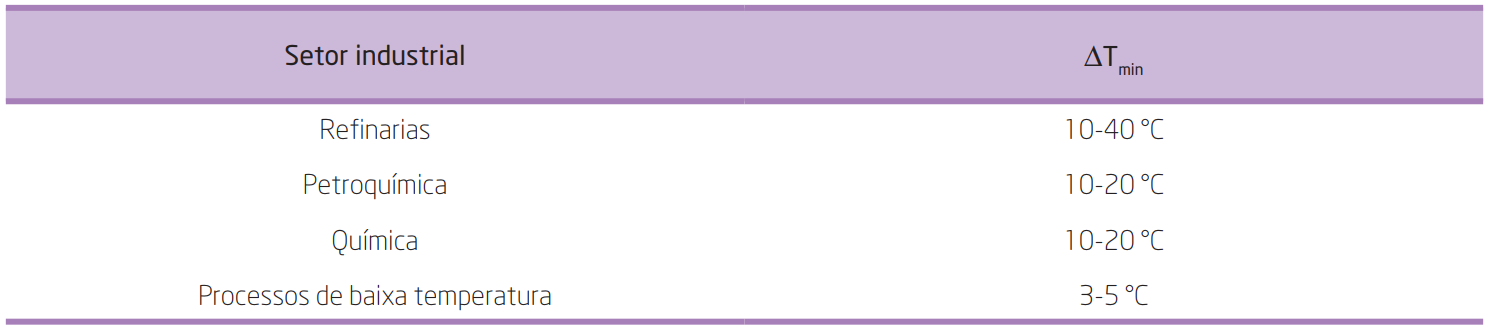
A Análise do Ponto de Estrangulamento, introduzida por Bodo linnhoff, é uma metodologia de integração energética que é de fácil aplicação e que se baseia na Primeira e na Segunda lei da Termodinâmica, permitindo analisar sistematicamente os processos químicos e os sistemas de utilidades. A Primeira Lei da Termodinâmica fornece a equação de energia para calcular as variações de entalpia nas correntes que passam através de um permutador de calor, enquanto a Segunda Lei determina a direção do fluxo de calor. ou seja, a energia térmica só pode fluir naturalmente na direção da fonte quente para um recetor frio. Num permutador de calor, nem uma corrente quente pode ser arrefecida abaixo da temperatura de fornecimento de fluxo frio, nem uma corrente fria pode ser aquecida a uma temperatura superior à temperatura de alimentação da corrente quente. Na prática, a corrente quente só pode ser arrefecida até uma temperatura definida pela diferença de temperatura mínima permitida, ∆Tmin (Figura 6.2).
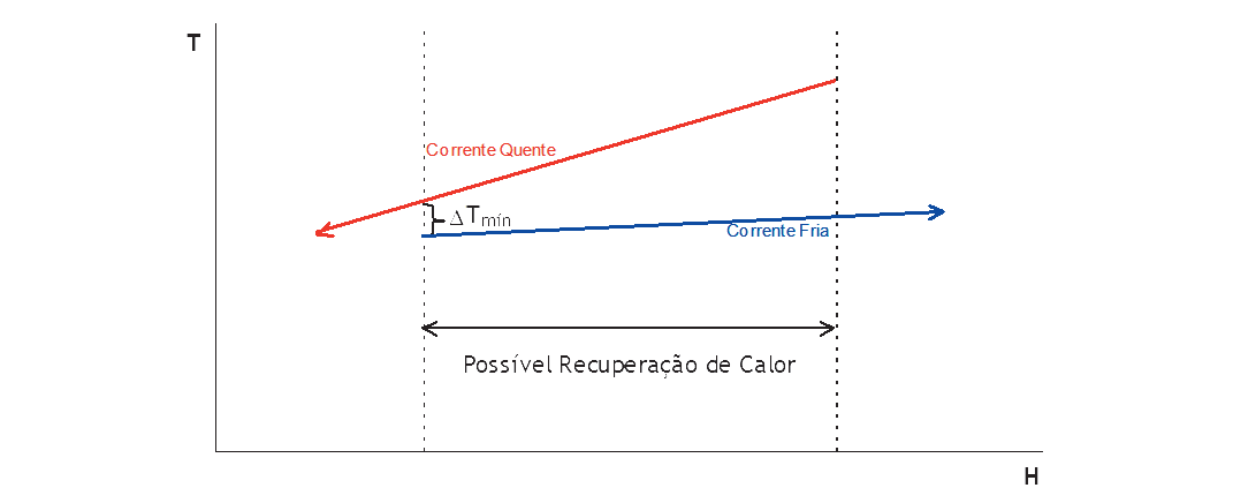
Figura 6.2 – Exemplificação esquemática do ΔTmin
A integração energética por aplicação da Análise do Ponto de Estrangulamento permite reduzir o consumo de utilidades exteriores ao processo, aproveitando os excessos entálpicos de correntes (correntes quentes) para fornecer às correntes com deficiência de entalpia (correntes frias). Após a integração, as correntes do processo deixam de permutar calor exclusivamente com as utilidades externas e passam a permutar calor também entre si. A aplicação da integração energética ao processo da Figura 6.1 permite obter um novo diagrama do processo, esquematizado na Figura 6.3. Assim, o objetivo principal da análise é conseguir poupanças financeiras através de uma melhor integração do calor do processo, maximizando a recuperação do calor do processo e reduzindo as utilidades externas.
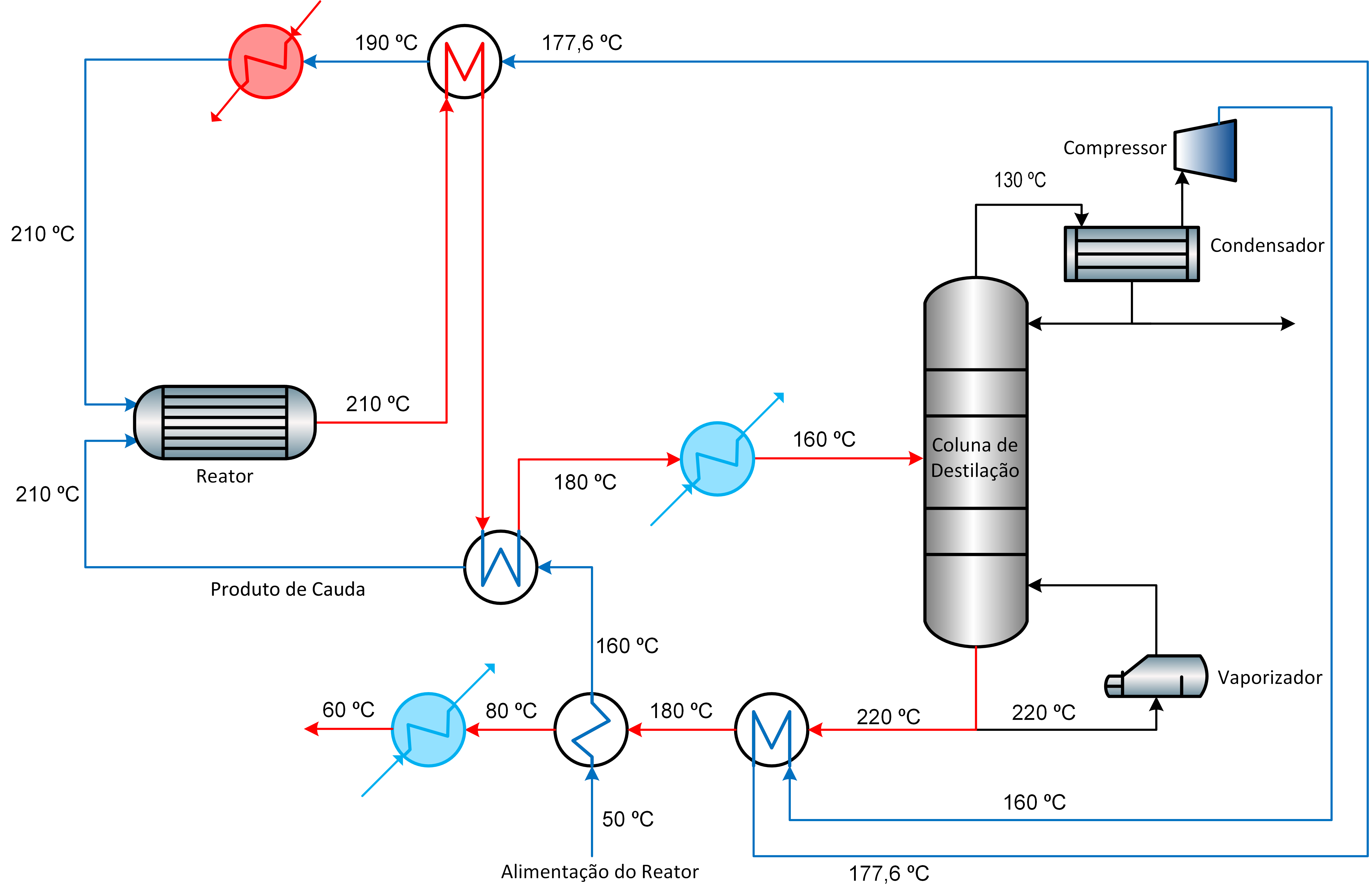
Figura 6.3 – Esquema do processo químico da Figura 6.1 com integração energética incorporada
O consumo total de energia reduz-se de 11 MW para 1,8 MW, embora este processo passe a apresentar sete permutadores de calor, em vez dos quatro existentes na Figura 6.1. No entanto, os custos globais anuais, calculados através da soma algébrica dos custos energéticos anuais e dos custos da amortização anual do investimento, apresentam uma redução de 50%.
Uma estratégia adequada para a aplicação da Integração Energética passa por quatro etapas essenciais:
- Recolha de dados e características sobre o processo e o sistema de utilidades;
- Determinação dos objetivos a alcançar de modo a maximizar o desempenho em diversos aspetos;
- Construção de uma rede de permutadores de calor;
- Simplificação da rede proposta para diferentes cenários económicos.
Existem vários softwares no mercado, a maioria não gratuitos, que permitem realizar estudos de Integração Energética, baseados na Análise do Ponto de Estrangulamento. uma parceria entre o IST e a ADENE permitiu desenvolver uma ferramenta computacional livre, a FI2EPI (Ferramenta Informática para Integração Energética de Processos Industriais, em português), com versões em português e inglês. A FI2EPI é uma ferramenta que recorre à Análise de Ponto de Estrangulamento e pode ser aplicada em instalações industriais com consumo de energia térmica, possibilitando o traçado automático das curvas compostas e da curva composta global do processo. Este software permite ainda a construção automática da rede de permutadores de calor correspondente ao consumo de energia mínimo e fazer a sua evolução para diminuir o custo global do processo 41.
6.2.2 Condicionantes à Integração Energética
O layout da unidade fabril pode impossibilitar algumas trocas de calor por envolver correntes que se distanciam bastante fisicamente, traduzindo-se em elevados custos de tubagem e bombagem, entre outros.
A segurança é também um fator a ter em consideração quando a troca de calor é efetuada entre correntes quimicamente incompatíveis, ou sempre que a corrente contenha produtos altamente poluentes ou perigosos.
A pureza do produto final pode eventualmente ficar comprometida se a operação final de purificação ficar sujeita a permuta de calor entre correntes, o que de alguma forma dificulta o controlo das condições operatórias que nesta unidade são mais exigentes, e pode também gerar potencialmente alguma contaminação.
Questões operatórias que possam estar em causa no arranque ou paragem da unidade poderão também ser condicionantes de certos cenários, bem como o controlo e a flexibilidade do próprio processo.
6.3 Bombas de Calor
A importância das bombas de calor para o aumento de eficiência e a redução de emissões tem sido crescente. Os mercados estão em expansão constante, mas em muitos países o foco é essencialmente no setor residencial para a regulação da temperatura ambiente ou para a distribuição de água quente 42.
As bombas de calor industriais (BCI’s), cada vez mais utilizadas, usam o calor residual do processo como fonte de calor, promovendo-o a uma temperatura superior, de tal forma que permita a sua utilização noutro local do processo, para aquecimento ou pré-aquecimento. Esta tecnologia tem como vantagem a redução significativa do consumo de combustíveis fósseis e da emissão de gases de efeito de estufa, por exemplo em processos de secagem, lavagem, evaporação, destilação e aquecimento e refrigeração de edifícios industriais e comerciais. As indústrias que podem beneficiar da implementação de bombas de calor incluem o processamento de alimentos e bebidas, produtos florestais, têxteis e químicos.
A implementação de bombas de calor industriais apresenta alguns problemas, como:
- Falta de refrigerantes no intervalo de temperatura pretendido;
- Tecnologia e equipamentos ainda pouco acessíveis e divulgados junto dos potenciais utilizadores;
- Incerteza na fiabilidade, por parte dos possíveis utilizadores.
No entanto, as BCI’s apresentam vantagens muito relevantes quando comparadas com as bombas de calor para aquecimento de espaços:
- Elevados coeficientes de desempenho (COP - coeficiente of performance);
- Elevada duração de operação;
- Baixo custo de investimento, devido à curta distância entre a origem de calor e destino;
- Procura de calor e produção de calor residual em simultâneo.
6.3.1 Conceitos Termodinâmicos
As bombas de calor usam energia externa para realizar trabalho de forma a efetuar a transferência de calor da fonte para o destino.
Como se pode verificar pela Figura 6.4 a fonte de calor residual encontra-se a um nível térmico inferior (TC) ao qual será usado (TH). Para tal, existe a necessidade de realizar trabalho para obter o calor a uma temperatura superior que permita a sua utilização noutro ponto do processo.
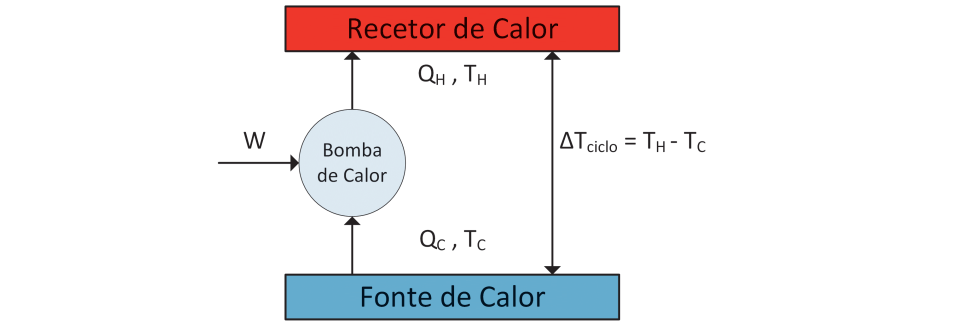
Figura 6.4 – Bomba de calor, transferindo calor de uma fonte fria para uma fonte quente à custa de trabalho
Com base na Primeira Lei da Termodinâmica, o calor transferido, QH à temperatura TH está relacionado com o calor extraído QC à temperatura TC e o trabalho realizado W, como está ilustrado na Equação (6.1).

As bombas de calor de compressão podem atingir um COP de 6, significando que um calor de 6 kWh pode ser produzido a partir de 1 kWh de energia elétrica de um compressor.

Apesar das vantagens das BCI’s, o número de instalações de bombas de calor na indústria é quase insignificante em comparação com as que estão instaladas para aquecimento de edifícios.
Ao comparar sistemas de bombas de calor com diferentes fontes de energia, é mais apropriado usar o rácio de energia primária (PER), descrito na Equação (6.3):

Este rácio relaciona-se com o COP através da eficiência (η), como é descrito pela Equação (6.4):

Onde η é a eficiência com que a energia primária é convertida em trabalho, através do compressor.
Se o processo onde a bomba de calor vai ser inserida for simples e composto por poucas correntes, em que a fonte e o destino estão bem definidos, pode não existir a necessidade de efetuar uma avaliação minuciosa. o estudo de apenas alguns parâmetros, como a temperatura, a carga térmica e as propriedades físicas, pode ser suficiente para garantir a fiabilidade do sistema.
Na indústria, a maioria das bombas de calor são utilizadas nas gamas de potência de 50 a 150 kW e 150 kW a 10 MW.
O parâmetro-chave para a escolha da bomba de calor industrial é a temperatura da fonte e de destino.
Os principais processos termodinâmicos para uma bomba de calor industrial são:
- Ciclo de compressão mecânica;
- Ciclo de compressão térmica;
- Recompressão mecânica a vapor (MVR);
- Recompressão térmica a vapor (TVR).
6.3.2 Ciclos de Compressão Mecânica
Na Figura 6.5 apresenta-se um esquema simplificado de ciclo de compressão fechado.
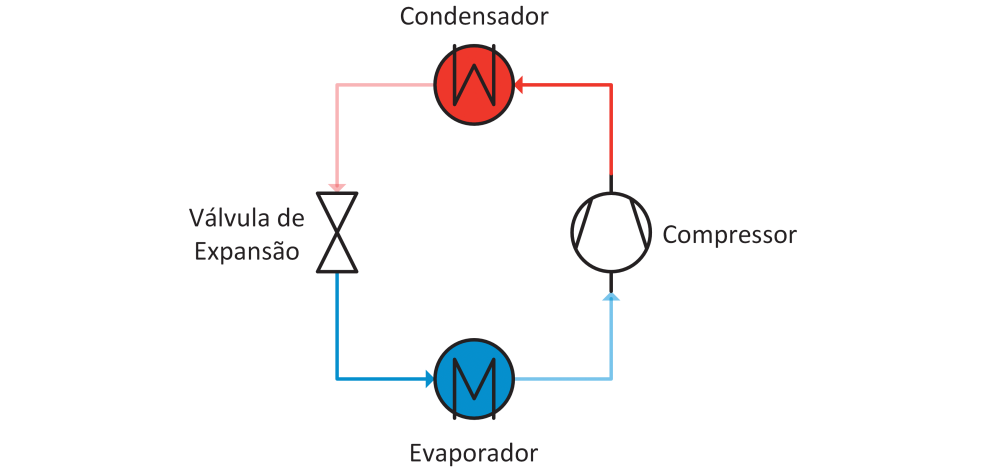
Figura 6.5 – Ciclo de compressão mecânica
As bombas de calor de compressão podem usar quatro tipos diferentes de compressores: espiral, pistão, parafuso-rotativo e centrífugo.
A escolha do tipo de compressor está relacionada com a quantidade de calor final. o compressor espiral é usado para um output até 100 kW, o compressor pistão até 500 kW, o compressor parafuso-rotativo até 5 MW e o compressor centrífugo usado em sistema de grandes dimensões acima de 2 MW 41.
6.3.3 Ciclos de Compressão Térmica
6.3.3.1 Bombas de calor de absorção
Enquanto uma bomba de calor mecânica opera a eletricidade, a de absorção opera a energia térmica, que pode ser obtida através de vapor ou pela combustão de gás natural. Este tipo de bombas de calor torna-se economicamente atrativa quando existe uma fonte de energia térmica barata a temperaturas de 100 a 200 °C, como energia geotérmica, energia solar ou calor excedente dos processos de cogeração ou centrais de vapor. Existem dois princípios-chave: absorção e evaporação do refrigerante. é comum usar o sistema Água (meio absorvente) – Amónia (refrigerante).
Na Figura 6.6 encontra-se um esquema simples deste tipo de tecnologia.
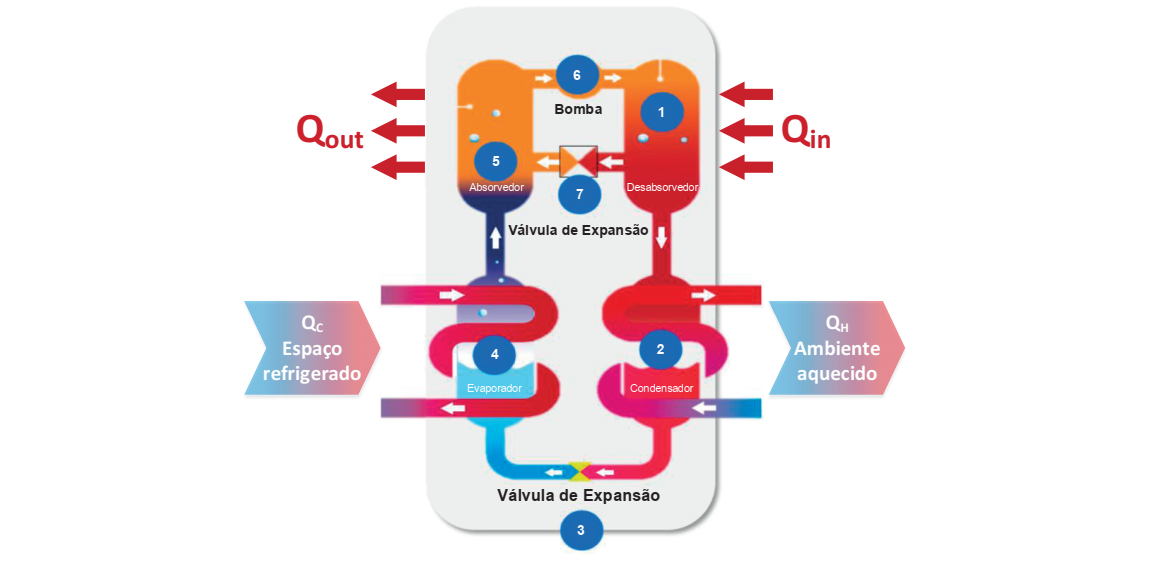
Figura 6.6 – Bomba de calor de absorção
FA energia térmica é fornecida ao desabsorvedor, o que faz com que o fluido refrigerante se evapore do meio absorvente. Por sua vez, o meio absorvente através de uma válvula é direcionado para o absorvedor. A absorção do fluido refrigerante gasoso acontece no absorvedor, provocando a libertação de calor. A mistura é redirecionada ao desabsorvedor através de uma bomba. De modo a aumentar a eficiência, efetua-se um pré-aquecimento da mistura fria com a mistura quente.
Devido ao uso de energia térmica para separar os dois componentes, o fluido refrigerante gasoso entra no condensador. Após a condensação, existe a libertação de calor e o fluido refrigerante líquido segue para uma válvula de expansão antes de entrar no evaporador. Com o fornecimento de calor, ocorre a evaporação do fluido refrigerante que segue para o absorvedor 42.
![]() |
Na produção de calor a uma temperatura de 70 °C, este sistema apresenta uma eficiência de 150%, ou seja, com 1 kWh de gás natural obtêm-se 1,5 kWh de calor. |
6.3.3.2 Bombas de calor de absorção-compressão
Este tipo de tecnologia engloba tanto o processo de absorção como o de compressão. Na Figura 6.7 encontra-se um esquema simplificado da tecnologia híbrida absorção-compressão.
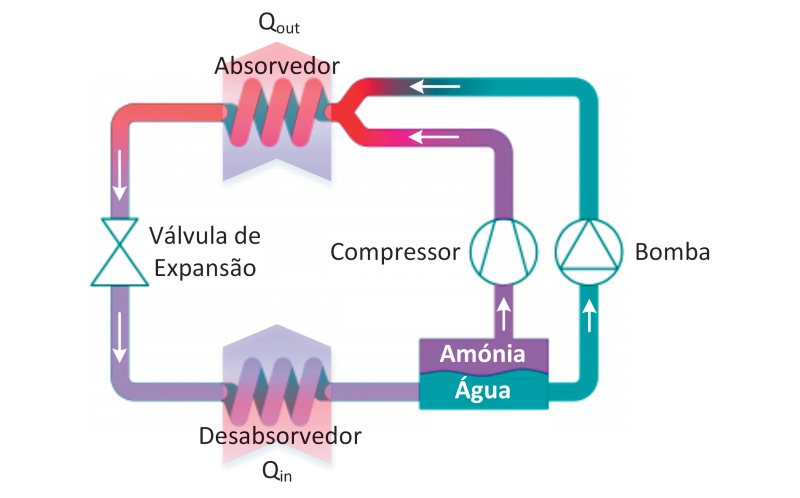
Figura 6.7 – Ciclo de absorção-compressão
A diferença entre o ciclo híbrido de absorção-compressão para o de absorção, é que no processo híbrido, a absorção ocorre a pressão e temperatura elevadas e a dessorção ocorre a pressão e temperatura baixa 42.
6.3.4 Recompressão Mecânica de Vapor (MVR)
Neste tipo de tecnologia, o vapor de baixa pressão proveniente de processos industriais (caldeiras ou evaporadores) é comprimido e condensado, gerando calor a uma temperatura mais elevada, podendo assim substituir uma fonte de energia exterior. Na Figura 6.8 está representado um esquema simplificado deste tipo de bomba de calor.
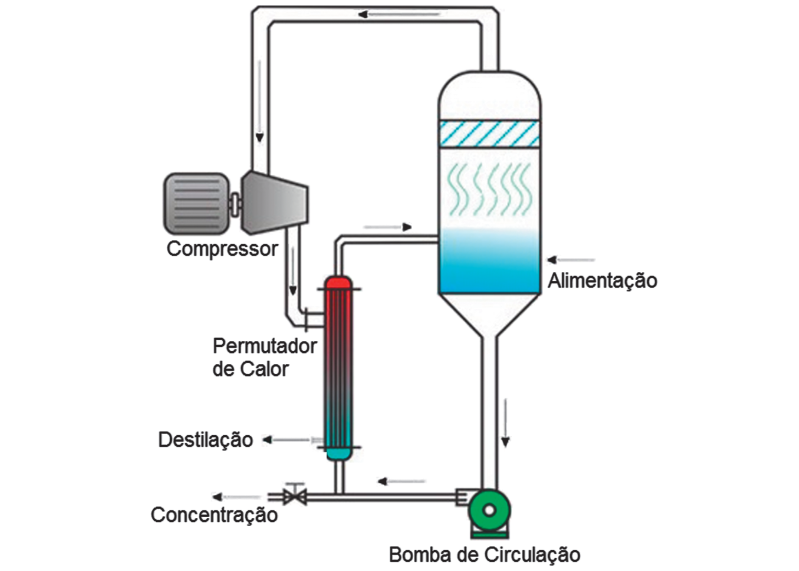
Figura 6.8 – Recompressão mecânica de vapor (MVR)
Caso o vapor se encontre contaminado, é necessário um permutador de calor intermédio (ebulidor). Neste caso diz-se que o sistema é semiaberto.
O COP para instalações de recompressão mecânica de vapor situa-se entre 10 a 30.
A recompressão mecânica é usada em operações de destilação, evaporação, secagem e para a produção de vapor para uma rede de distribuição de vapor 42.
6.3.5 Recompressão Térmica de Vapor (TVR)
Neste tipo de tecnologia o vapor é comprimido num ejetor e ao contrário da recompressão mecânica, não é necessário o uso de energia mecânica. Pode ser usado em inúmeras aplicações, em que exista uma diferença significativa entre os preços dos combustíveis e o da eletricidade. Tal como a recompressão mecânica, também pode ser usada em unidades de evaporação.
Na Tabela 6.2 encontra-se um resumo das principais tecnologias de bombas de calor industriais, bem como os parâmetros de temperatura da fonte e a temperatura a que se consegue produzir o calor.
Tabela 6.2 – Gama de temperaturas em bombas de calor industriais

Em algumas situações, o sistema TVR pode permitir a produção de calor a níveis térmicos elevados, cerca de 200 °C 42.
6.4 Aproveitamento do Excesso Entálpico de Baixa Temperatura
Muitos dos processos industriais possuem necessidades entálpicas numa gama de temperaturas de 90 a 120 °C e têm disponíveis fontes de calor residuais com temperaturas entre 30 e 60 °C. A aplicação de bombas de calor para colmatar as necessidades entálpicas seria muito útil, reduzindo o consumo energético específico (por quantidade de produto final). Atualmente, muitos refrigerantes encontram-se restringidos a temperaturas que não permitem o fornecimento de fluxos de calor às temperaturas indicadas. Têm sido, por esta razão, desenvolvidos refrigerantes que possam cobrir estas necessidades, tendo em conta não só as propriedades termodinâmicas como o ponto de ebulição, mas também, por exemplo o potencial de aquecimento global (Global Warming Potential, GWP), que em muitos refrigerantes atuais é relativamente elevado.
O excesso entálpico de uma corrente (gás, água, ar, etc) é a entalpia da corrente que não tem uso direto no processo num determinado momento. Todo o excesso entálpico que for possível reutilizar, técnica e economicamente, deverá ser tido em conta.
Existem três tecnologias para recuperação/reutilização de excesso entálpico:
- Uso direto;
- Bombas de calor;
- Produção de energia elétrica.
O uso direto quer dizer que o calor sensível ou latente, não é enriquecido através de uma bomba de calor, pelo que pode ser armazenado.
A seleção da tecnologia de recuperação de calor depende de fatores como:
- Temperatura;
- Fase física;
- Composição da corrente.
O excesso de calor industrial a baixas temperaturas, inferiores a 50 °C, costuma ser usado por exemplo, para o aquecimento de estufas ou na produção de comida.
A produção de energia piezoelétrica é uma opção para utilizar excesso de calor a baixas temperaturas (100 – 150 °C), embora tenha uma eficiência baixa (1%) e custos de investimento elevados.
No geral, a produção de energia através de excesso de calor, está limitada a temperaturas médias/altas. No entanto, devido ao avanço tecnológico nos ciclos de energia, tem sido possível aumentar a fiabilidade da produção de energia a baixas temperaturas. Embora as eficiências sejam baixas, estes sistemas podem ser economicamente interessantes, se a quantidade de calor a recuperar for elevada.
O Ciclo de Rankine Orgânico (CRO), opera de forma semelhante ao ciclo de Rankine com vapor, mas usa um fluido orgânico em vez de vapor. o intervalo de temperaturas do CRO irá depender do fluido usado, das propriedades termodinâmicas do fluido que vão influenciar a eficiência do ciclo. O CRO usa um fluido orgânico de alta massa molecular como por exemplo silicone, propano, isopentano, isobutano, p-xileno e tolueno.
O fluido permite a recuperação do calor do ciclo de Rankine de fontes a temperaturas baixas. o calor de baixas temperaturas é convertido em trabalho útil, e posteriormente transformado em eletricidade.
Apesar da elevada eficiência de turbina (80 - 85%), a eficiência global do CRO é somente de 10-20%, dependendo da temperatura do condensador e evaporador.
- 40 B. lloyd, “7 Tips for cleaning heat exchangers”, Process Heating, vol. 21, nº 5, 2014.
- 41 J. Klemes, “Handbook of Process Integration (PI) - Minimisation of Energy and Water use, Waste and Emissions”, First Edition, Woohead Publishing, 2013.
- 42 Office of Energy Efficiency & Renewable Energy, “Waste Heat Recovery: Technology and opportunities in U.S. Industry”