Capítulo 4
Produção de Calor e Frio
A produção de calor e frio são habitualmente duas componentes de energia térmica que permitem o funcionamento dos Processos Industriais. O calor, sendo energia em movimento, pode ser obtido pela combustão direta de combustíveis fósseis ou não fósseis. Apesar de, em termos ambientais, ser preferível usar esta última forma de energia primária, neste momento tal não é muitas vezes possível dentro do quadro do atual desenvolvimento económico-tecnológico. Nestas circunstâncias, devem ser adotadas medidas que melhorem os sistemas de queima, bem como o aumento da eficiência energética nos sistemas de produção e distribuição de vapor de água. Este fluido é a utilidade quente mais utilizada na indústria transformadora, e toma por isso mesmo um lugar de destaque em termos de enumeração das medidas de melhores práticas para a sua utilização. O sistema de frio é usualmente obtido através de equipamentos de compressão e evaporação que recorrem também ao consumo de energia elétrica, utilizando fluidos refrigerantes.
4.1 Sistemas de Combustão
Nos sistemas baseados em combustível, o calor é obtido por combustão direta ou indireta de combustível sólido, líquido ou gasoso. Os gases de combustão podem estar em contacto com o material (aquecimento direto), ou serem confinados e, portanto, separados do material (aquecimento indireto – exemplo: tubo de queimador radiante, retorta, etc.). Exemplos de equipamentos de aquecimento de processos baseados em combustível incluem fornalhas e caldeiras.
Os sistemas de combustão estão na origem da maior parte do calor que é utilizado na concretização dos Processos Industriais. Assim, neste tópico são apresentadas algumas das melhores técnicas disponíveis (equivalente à sigla inglesa BAT – Best Available Techniques) para aumentar a eficiência energética em sistemas de combustão. Estas técnicas são tão válidas para sistemas de chama (com queimadores), como para sistemas de combustão em leitos fluidizados 25.
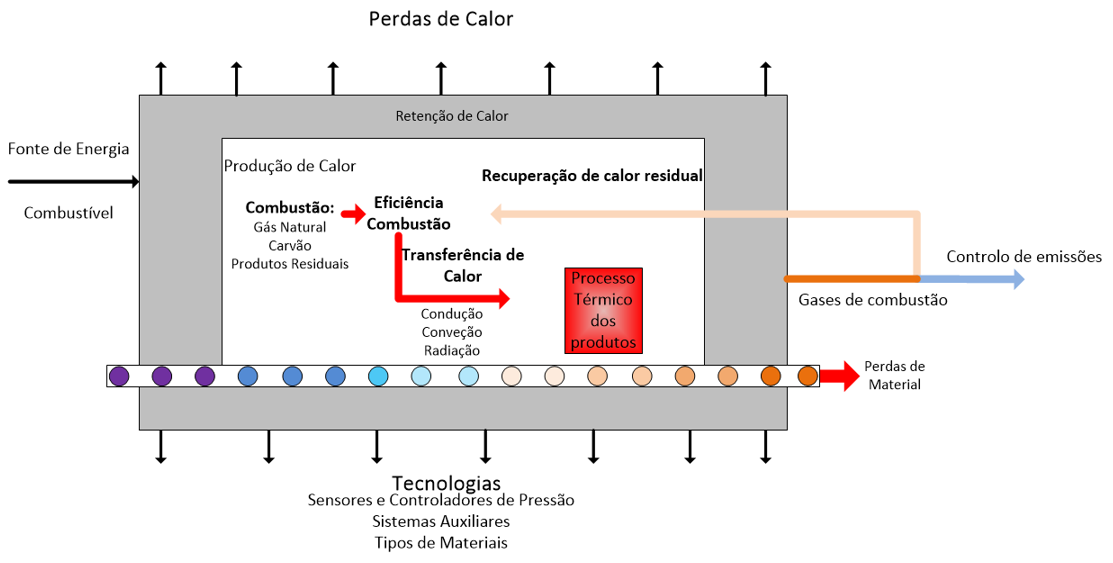
Figura 4.1 – Esquema geral de um sistema de queima
Neste subcapítulo são analisadas as melhores tecnologias relacionadas com fornalhas, caldeiras e fornos, bem como com os respetivos modos de operação industrial.
Apesar de algumas das técnicas aqui apresentadas também se aplicarem a sistemas de vapor, o aumento da eficiência energética destes últimos será alvo de atenção específica na secção 4.1.3.
4.1.1 Diminuição das Perdas Térmicas num Sistema de Combustão
Num sistema de combustão que teoricamente apresente uma eficiência energética de 100%, toda a energia libertada na queima do combustível é transferida para o processo de destino. No entanto, estes sistemas ideais não existem, pelo que parte dessa energia é dissipada para o meio envolvente através das paredes e dos gases de combustão, como se encontra exemplificado na Figura 4.2.
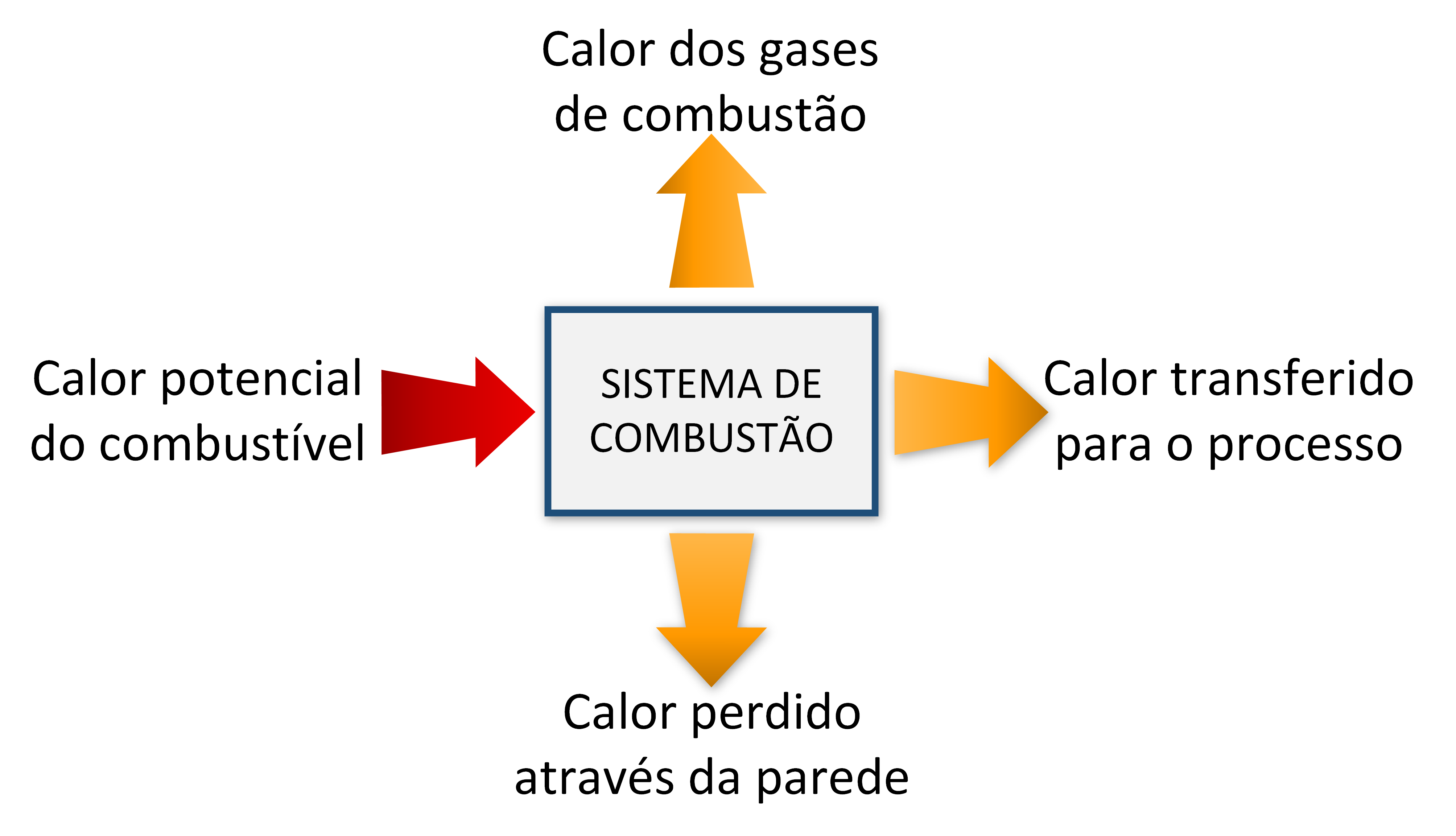
Figura 4.2 – Balanço de conservação de energia a um sistema de combustão genérico
De acordo com a Figura 4.2, a eficiência energética (η) de um sistema de combustão é dada pela Equação (4.1) ou (4.2).

A definição de eficiência energética expressa pela Equação (4.2) indica que as estratégias tecnológicas para o aumento da eficiência devem ser orientadas para a diminuição das perdas térmicas através das paredes e dos gases de combustão.
A diminuição das perdas térmicas pode ser conseguida através de:
- Redução da temperatura de saída dos gases de combustão;
- Diminuição do caudal mássico dos gases de combustão;
- Substituição de isolamentos térmicos danificados e aplicação de isolamentos mais eficazes.
4.1.1.1 Redução da temperatura de saída dos gases de combustão
As principais estratégias para reduzir a temperatura de saída dos gases de combustão são:
- O aumento da área ou da taxa de transferência de calor;
- A integração energética de modo a alimentar processos que necessitem de calor;
- O pré-aquecimento do ar de entrada dos sistemas de combustão;
- A limpeza e manutenção das superfícies de transferência de calor de modo a evitar a deposição de resíduos sólidos.
![]() |
O aumento de 1 mm do fouling nas superfícies de permuta de calor pode levar a um aumento de 2% no consumo de combustível. |
![]() |
A diminuição de 20 °C na temperatura nos gases de saída das caldeiras pode levar a um aumento de cerca de 1% na eficiência energética do sistema. |
No entanto, as estratégias de redução da temperatura dos gases de combustão devem respeitar alguns requisitos:
- Só se procede à recuperação do calor excedentário dos gases se existirem pontos nas proximidades disponíveis para o receber;
- Nos sistemas com combustíveis que tenham elevado teor de enxofre, a temperatura de saída dos gases não deverá ser inferior à temperatura de condensação da mistura de água e ácido sulfúrico, encontrando-se normalmente entre 110 e 170 °C, dependendo essencialmente da percentagem de enxofre presente.
![]() |
As estratégias acima descritas requerem um investimento adicional e são melhor aplicadas no design e construção da instalação. O retorno do investimento situa-se entre os 5 e os 15 anos. |
4.1.1.2 Diminuição do caudal mássico dos gases de combustão
A diminuição do caudal mássico dos gases de combustão é conseguida através da redução do excesso de ar à entrada da instalação de combustão. Este excesso de ar pode ser minimizado através do ajuste proporcional do fluxo de ar em relação ao de combustível.
![]() |
A minimização do excesso de ar leva a uma menor emissão de NOx. |
![]() |
É necessário garantir a quantidade estequiométrica de oxigénio necessária a uma combustão total e evitar atmosferas explosivas. Por motivos de segurança e ambientais, a combustão deve sempre decorrer numa atmosfera com pelo menos 5% de excesso de ar. |
4.1.1.3 Uso de isolamentos térmicos mais eficazes e substituição de isolamentos danificados
De modo a minimizar as fugas de calor através das paredes de uma instalação de combustão, a eficiência do isolamento térmico deve ser assegurada durante a fase de projeto da instalação. No entanto, os isolamentos térmicos degradam-se, e por isso, devem ser implementados programas de inspeção, manutenção e substituição dos mesmos. Existem algumas técnicas (p. ex., infrared imaging) que podem ser usadas para diagnosticar a partir do exterior, zonas mal isoladas. Informação mais detalhada sobre isolamentos pode ser consultada na Secção 8.4.
![]() |
O uso de isolamento deficiente e/ou um projeto desatualizado pode levar a perdas de calor por radiação de 10% (os valores normais representam cerca de 1%). |
4.1.2 Tecnologias de Combustão com Ar a Temperaturas Elevadas (HiTAC)
Na tecnologia de fornalhas convencional, cerca de 70% do calor produzido é perdido no gás de escape a temperaturas de 1300 °C. Com o objetivo de recuperar estas perdas de calor têm-se desenvolvido sistemas com recuperadores ou regeneradores cerâmicos, sendo estes os equipamentos que mais contribuem para o aumento da eficiência energética em sistemas de combustão 32.
Um recuperador é um permutador de calor que extrai calor dos gases de combustão com o objetivo de pré-aquecer o ar de entrada. Nos queimadores auto-recuperativos, Figura 4.3, o recuperador faz parte do queimador, diminuindo os custos em relação à opção de ter um queimador e um recuperador em separado, facilitando também a reconversão dos sistemas de combustão já existentes.
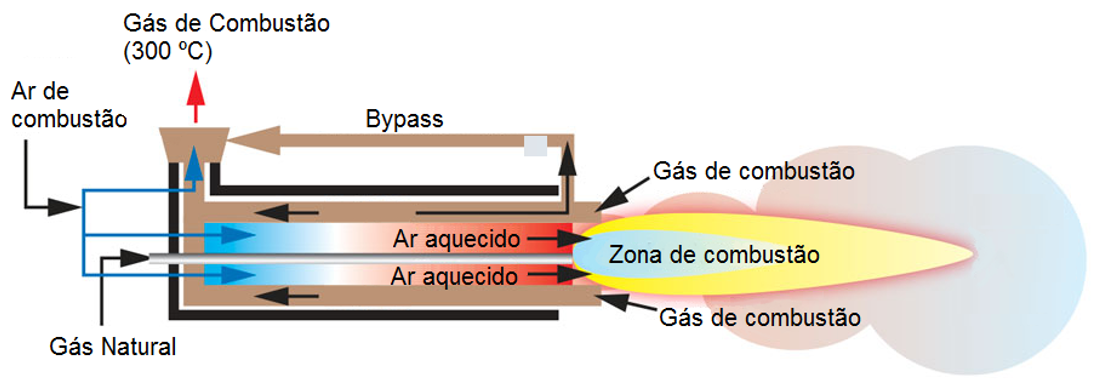
Figura 4.3 – Esquema de um queimador auto-recuperativo 33
![]() |
Comparado com o sistema convencional, a colocação de um recuperador de calor leva a um aumento da eficiência energética em 30% 26. |
Os queimadores regenerativos, Figura 4.4, operam em pares, enquanto um queima o combustível, o outro armazena calor num leito cerâmico poroso. Cada queimador opera pelo período entre 30 a 60 segundos, invertendo os papéis após o ciclo de operação. Em termos energéticos, é recuperado cerca 85 a 90% do calor dos gases de combustão 32. O pré-aquecimento do ar de entrada é feito até 100 a 150 °C abaixo da temperatura de operação interna do sistema de combustão.
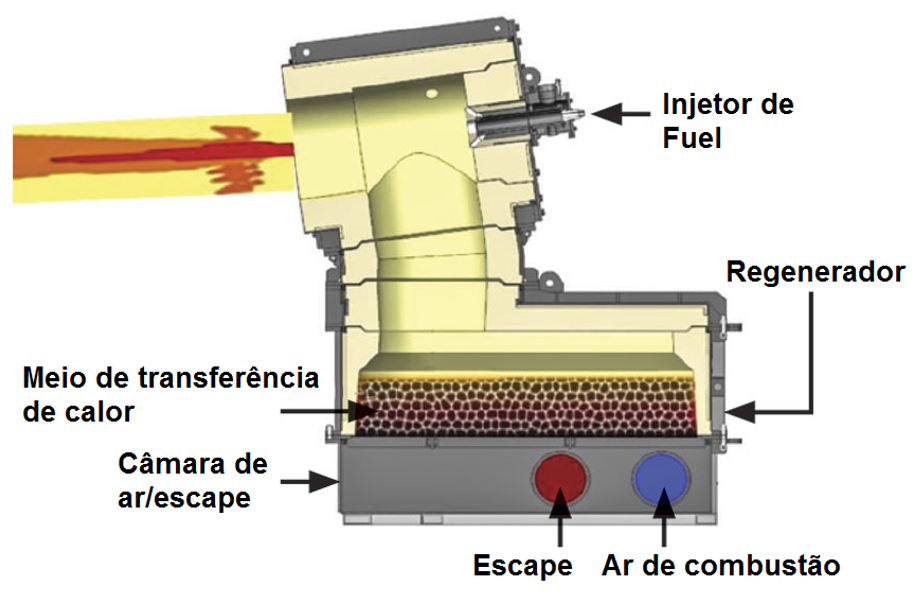
Figura 4.4 – Esquema de um queimador regenerativo 33
![]() |
A redução do consumo de combustível pode atingir entre os 50 e 60% 26. |
![]() |
Embora o pré-aquecimento de ar de entrada aumente a eficiência energética da combustão, leva a um aumento da temperatura de chama e consequentemente tende a promover maiores produções de NOx , cujos custos de tratamento (remoção catalítica) são elevados. |
Nesta área, têm sido desenvolvidos estudos centrados na utilização de queimadores auto-recuperativos e de recuperadores cerâmicos para altas temperaturas. Estes desenvolvimentos visam sempre a eficiência energética aliada à minimização das emissões de NOX.
Com a tecnologia HiTAC, o ar de combustão é pré-aquecido a temperaturas bastante elevadas antes da injeção na fornalha a alta velocidade, permitindo a queima total de combustível, mesmo na presença de baixos teores de oxigénio. As principais vantagens desta tecnologia são 34:
- Perfil de temperaturas mais uniforme no interior da câmara de combustão;
- Emissões reduzidas de NOX;
- Maior durabilidade do sistema de combustão (fornalha e tubagens);
- Aumento da produtividade e qualidade do produto;
- Maior eficiência energética com redução das emissões de CO2;
- Baixas emissões de CO e NOx;
- Aumento da transferência de calor;
- Dispensa de outros equipamentos para aumentar a economia energética nos sistemas de combustão;
- Aumento da produtividade e qualidade do produto (se o sistema de combustão fizer parte de um processo produtivo).
![]() |
A implementação deste sistema envolve um grande investimento. A diminuição dos custos de energia por si só raramente compensa o investimento, logo, deve-se considerar a maior produtividade na fornalha e a redução de emissões na análise custo-benefício. |
4.1.3 Aumento de Eficiência Energética de Fornalhas e Fornos
Neste tópico são referidos os equipamentos que geram calor através da queima de combustíveis e transferem-no para um determinado processo 25.
Os principais sistemas de produção de calor na indústria são:
- Fornalhas para produção de calor por queima de combustível;
- Fornos para cozedura e calcinação.
As principais medidas a considerar com vista ao aumento da eficiência energética dos sistemas de combustão são apresentadas em seguida.
Fornalhas:
- Controlar o rácio ar/combustível;
- Redução do excesso de ar
- Pré-aquecimento do ar de combustão ou oxidante
- Excesso de oxigénio
- Melhorar o armazenamento, preparação e distribuição do combustível;
- Instalar e inspecionar isolamentos térmicos.
![]() |
O controlo do rácio ar/combustível leva a um aumento da eficiência entre 5 a 25%. O pré-aquecimento do ar de combustão origina uma melhoria de 15 a 30%. Usar excesso de oxigénio, proporciona um aumento de eficiência entre 5 a 25%. |
Deve-se ter em conta também possíveis perdas de ar de combustão a jusante da válvula de controlo, controlar a mistura ar/ combustível nas condições de funcionamento do equipamento e verificar o excesso de oxigénio nos gases de combustão, pois este parâmetro indica que se está a usar um excesso de ar superior ao necessário.
Fornos:
- Efetuar a manutenção adequada dos isolamentos, reparação de fugas e limpeza dos queimadores;
- Controlar a combustão através da análise dos gases de combustão (regulação do excesso de ar);
- Verificar os sistemas de controlo de combustão;
- Efetuar a programação das cargas
4.2 Eficiência Energética nos Sistemas de Produção e Distribuição de Vapor
As principais medidas para aumentar a eficiência energética em sistemas de produção e distribuição de vapor são as seguintes 25:
- Utilização de permutadores de calor, denominados de economizadores, para pré-aquecer a água de alimentação à caldeira;
- Remoção de depósitos de calcário e/ou fuligens das superfícies de transferência de calor;
- Minimização de purgas da caldeira;
- Recuperação do calor das purgas;
- Reutilização do vapor de flash (p. ex., vapor gerado por expansão de condensados);
- Isolamento de tubagens, válvulas e flanges;
- Eliminação de fugas de vapor e condensados;
- Programa de controlo e manutenção dos purgadores;
- Remoção preventiva de depósitos nas superfícies de transferência de calor.
4.2.1 Utilização de Economizadores para Pré-aquecimento de Água de Alimentação
A colocação de um economizador à saída dos gases de combustão permite o pré-aquecimento da água de alimentação da caldeira. O teor de enxofre do combustível vai ter um grande impacto na corrosão dos equipamentos, pelo que o design do economizador deve permitir uma troca fácil das peças que estão sujeitas a corrosão.
![]() |
A utilização destes equipamentos em caldeira com gases de combustão a 230 °C, leva a um aumento da eficiência global em cerca de 4%, sendo uma opção para produções de vapor acima de 10 ton/h 25. |
4.2.2 Remoção Preventiva de Depósitos nas Superfícies de Transferência de Calor
Esta ação consiste na remoção química ou mecânica de depósitos sólidos e numa possível reformulação do sistema de tratamento de águas caso a necessidade de limpeza se torne demasiado frequente. O inconveniente da limpeza mecânica é que só pode decorrer durante os períodos de paragem programados 25.
Um eventual reajuste na pressão de vapor também é uma hipótese a ter em conta, pois menores pressões implicam menores temperaturas o que leva a uma redução na formação de depósitos.
![]() |
1 mm de espessura na superfície metálica dos permutadores de calor representa uma diminuição de 9% na transferência de calor através dessa superfície. |
4.2.3 Minimização de Purgas das Caldeiras
A diminuição do caudal de purga das caldeiras reduz substancialmente as perdas energéticas, os custos de tratamento da água de alimentação e os custos de tratamento associados às purgas 25.
As duas principais medidas para minimizar a quantidade de água e a energia desperdiçadas nas purgas, são as seguintes:
- Recolha dos condensados e reciclagem dos mesmos à caldeira. Se metade dos condensados forem reutilizados, as purgas são reduzidas em 50%;
- Pré-tratamento da água de alimentação das caldeiras para remoção de impurezas e iões indesejados, através de permuta iónica ou de processos de membranas (p. ex., osmose inversa). No entanto, no tratamento de águas duras, comuns no Centro e Sul de Portugal, a utilização de processos de membranas pode causar problemas de colmatação, por isso, a análise caso a caso é aconselhada.
4.2.4 Recuperação de Calor nas Correntes de Purga
o calor recuperado pode ser utilizado para o pré-aquecimento da água de alimentação das caldeiras. A purga pode ser também alimentada a um tanque flash de produção de vapor, onde o vapor gerado pode ser utilizado no desarejador da água de alimentação. Esta técnica é economicamente viável para valores de caudais de purga a partir de 5% do caudal de vapor produzido pela caldeira 25.
4.2.5 Implementação de Programas de Controlo, e Manutenção de Purgadores
A implementação de programas de inspeção e manutenção regulares dos purgadores de um sistema de vapor possibilita a obtenção de elevadas economias energéticas. os sistemas de vapor com frequência de inspeção superior a 3 anos possuem frequentemente um número elevado de purgadores defeituosos (até 30% do número total) que conduzem a perdas elevadas de vapor. Em contrapartida, nos sistemas com programas de inspeção e manutenção regulares, os purgadores com fugas constituem normalmente menos de 5% do número total.
![]() |
Embora os purgadores tenham tempos de vida útil muito curtos, os custos associados à substituição de purgadores defeituosos é sempre muito inferior ao custo dasperdas de vapor que podem ocorrer |
4.2.6 Recolha de Condensados para Reutilização na Caldeira
Esta técnica apresenta as seguintes vantagens imediatas:
- Redução da quantidade de água a tratar;
- Diminuição do consumo de combustível (os condensados têm uma energia térmica maior do que a água de alimentação fresca);
- Redução do caudal de purgas das caldeiras.
4.2.7 Utilização de Vapor Flash
A recuperação do vapor flash representa uma economia de energia bastante superior à que se verifica com a simples recuperação de condensados, principalmente para condensados a alta pressão, porque o vapor flash destes condensados contém um valor energético muito elevado. Este vapor pode ser utilizado no desgaseificador e/ou no pré-aquecimento de ar.
A recuperação de condensados a baixa temperatura também permite a obtenção de vapor flash que pode ser utilizado no aquecimento de componentes a temperaturas inferiores a 100 °C, por exemplo, água para banhos.
4.2.8 Isolamento Térmico no Sistema de Produção e Distribuição de Vapor
O reforço ou reparação dos isolamentos térmicos é justificado e conduz a economias energéticas significativas, se existir uma diferença mínima de 50 °C entre a temperatura da superfície exterior do equipamento e a do meio ambiente.
As perdas de calor que se verificam em válvulas e flanges não isoladas equivalem a perdas de calor em vários metros de tubagem não isolada. Por exemplo, as perdas numa válvula não isolada são idênticas às que se verificam num metro de tubagem não isolada com o mesmo diâmetro enquanto que as que se verificam numa flange não isolada são metade do valor atrás indicado. Informação mais detalhada pode ser consultada na Secção 8.4.
4.2.9 Instalação de um Pré-aquecedor de Ar
Entre as vantagens do pré-aquecimento do ar (através dos gases de combustão) encontram-se as seguintes:
- Por cada 20 °C adicionais que são retirados aos gases de saída, a eficiência da caldeira aumenta em 1%;
- O ar aquecido pode ser utilizado na secagem de combustível, nomeadamente se este se tratar de carvão ou matéria orgânica (biomassa), ou ser utilizado como ar de combustão;
- O pré-aquecimento permite ter caldeiras mais pequenas.
No entanto, algumas desvantagens práticas ocorrem também, entre as quais:
- A permuta de calor entre gases e ar é pouco eficiente, requerendo grandes áreas de permuta;
- A queda de pressão adicional que se verifica nos gases de combustão pode ser significativa, o que implica um aumento da pressão a fornecer pelo ventilador de extração;
- A utilização de ar mais quente, transportando menos oxigénio por unidade de volume que o ar que não é aquecido, requer uma adaptação/readaptação dos queimadores.
4.2.10 Medidas de Controlo e Manutenção
Para o bom funcionamento de uma caldeira, devem ser executadas as seguintes operações:
- A produção de vapor na caldeira deve ser medida, direta ou indiretamente, medindo-se o total da água de alimentação e calculando as quantidades perdidas nas descargas de fundo da caldeira. A relação vapor-combustível é a melhor medida de eficiência da caldeira e deve ser mantida a um nível elevado;
- Um registo permanente da eficiência da caldeira deve ser mantido de modo que os sinais de mau funcionamento possam ser detetados com antecedência;
- Os contadores de vapor devem ser examinados periodicamente, pois deterioram-se com o tempo. Se a pressão de operação for alterada, o contador deverá ser recalibrado ou, alternativamente, as leituras realizadas devem ser corrigidas;
- O sistema de tubagem deve ser vistoriado regularmente;
- As tubagens fora de uso devem ser isoladas ou retiradas se redundantes;
- O cálculo do consumo e do fornecimento de energia à casa das caldeiras deve ser o mais realista possível;
- A manutenção da casa de caldeiras deve ser revista, principalmente no que diz respeito ao equipamento de combustão, ao controlo e aos instrumentos. Deve adotar-se uma rotina de verificação regular;
- A limpeza periódica das superfícies de transferência de calor ou dos tubos de fumo deve ser mantida;
- O estado das alvenarias e do sistema de exaustão das caldeiras deve ser verificado periodicamente;
- As canalizações subterrâneas de exaustão devem ser inspecionadas com vista a possíveis infiltrações de água, especialmente em instalações de caldeiras mais antigas;
- As fugas de vapor e de ar comprimido devem ser prontamente reparadas de modo a evitar desperdícios de energia e potenciais acidentes.
4.2.11 Minimização de Perdas em Ciclos Curtos de Funcionamento das Caldeiras
Este ponto tem importância quando a caldeira estiver sobredimensionada, ou seja a funcionar a 25% da sua capacidade nominal ou menos) e/ou a funcionar apenas ocasionalmente. Estas perdas energéticas podem ser minimizadas através da substituição de uma caldeira por duas outras mais pequenas, podendo estar apenas uma em stand-by.
4.3 Sistemas de Produção de Frio Industrial
Os sistemas de refrigeração são cada vez mais utilizados em Portugal, principalmente no acondicionamento alimentar (p. ex., carnes, vegetais e frutas), para além de constituírem a componente de frio dos sistemas de ar condicionado, atualmente em forte expansão. Estes sistemas são caracterizados por um elevado consumo energético resultando em custos de operação elevados.
Os equipamentos de refrigeração devem ser concebidos de modo a que possam funcionar em condições variadas, de acordo com as exigências dos produtos a acondicionar, devendo funcionar eficientemente do ponto de vista energético, levando a uma redução dos custos de operação.
A Figura 4.5 apresenta um esquema de um circuito de refrigeração por compressão de vapor.
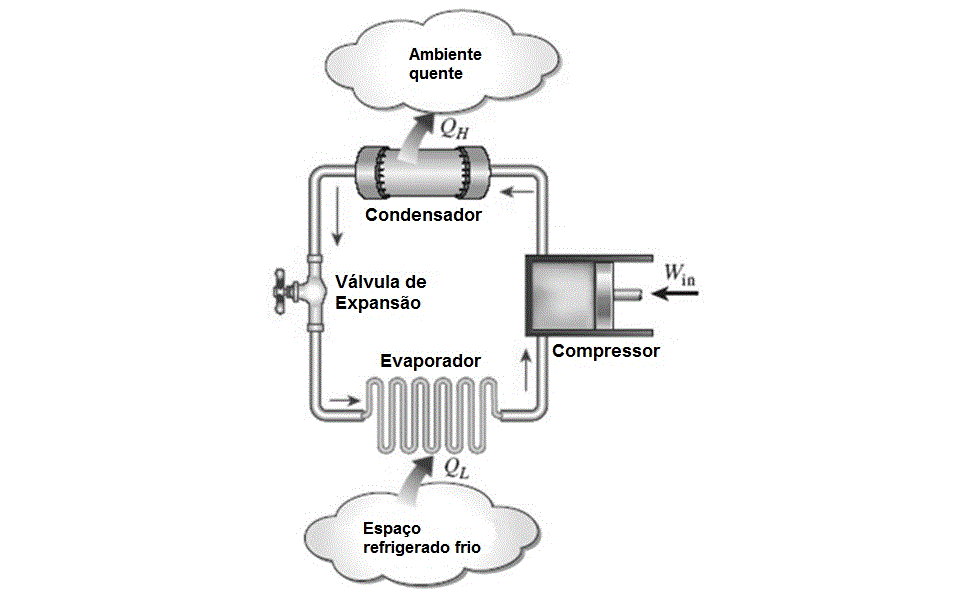
Figura 4.5 – Esquema de um ciclo de refrigeração 35
Os principais componentes de um sistema de refrigeração são:
Compressor – o vapor à saída do evaporador é comprimido até à pressão do condensador, para que o condensador funcione de forma eficiente;
Condensador – o vapor comprimido arrefece e condensa;
Válvula de expansão – o condensado é expandido, arrefecendo significativamente, devido ao efeito Joule-Tomson;
Evaporador – o refrigerante a baixa temperatura evapora retirando calor, obtendo-se o efeito de arrefecimento local.
A maior parte da refrigeração industrial é efetuada através de sistemas de refrigeração por compressão mecânica. Em alguns casos, são usados sistemas de refrigeração por absorção.
![]() |
Os sistemas de refrigeração consomem elevadas quantidades de eletricidade podendo ser responsáveis por 85% do consumo total de energia, dependendo d setor industrial 28. |
4.3.1 Sistemas Alternativos para a Produção de Frio
A aplicação de novos sistemas de refrigeração inclui a utilização de:
- Bombas de calor de absorção;
- Novos fluidos criogénicos (p. ex., amoníaco, CO2);
- Acumulação térmica de frio através de energia latente.
A definição das limitações do sistema de refrigeração que se encontra instalado numa dada fábrica é um ponto crucial, para a obtenção da solução que mais contribui para o aumento da eficiência energética.
![]() |
|
4.3.1.1 Melhorar a eficiência de um sistema já instalado
Muitas vezes um sistema de refrigeração é ineficiente porque opera em condições diferentes daquelas para as quais foi dimensionado. Assim, é possível melhorar o sistema de refrigeração através de 36:
- Revisão das necessidades de refrigeração;
- Revisão da instalação;
- Alteração do sistema de distribuição do refrigerante;
- Controlo da fábrica e set-points;
- Otimização da manutenção.
É bastante importante identificar no processo que etapas são críticas para o consumo de frio, bem como se é possível agrupar essas etapas, de modo a facilitar a operação do sistema. uma instalação de refrigeração pode ter muitos problemas, tais como:
- Tubagens mal colocadas e não isoladas;
- Permutadores de calor inadequados;
- Má instalação de equipamentos;
- Infiltração de ar.
Outro aspeto importante é a quantidade de produção de frio industrial, isto é, convém que a oferta (quantidade produzida pelo sistema refrigerante) seja, o mais possível, próxima da procura (quantidade necessária para o bom funcionamento da instalação). Caso contrário a instalação encontra-se a produzir excesso de fluido refrigerante, que, ao não ser utilizado de forma útil no processo, é classificado como uma perda e prejuízo.
Desta forma, a carga de frio está diretamente relacionada com a melhoria da eficiência do sistema de refrigeração. Por exemplo, se a temperatura de um produto ao chegar ao sistema de refrigeração for superior à desejada, vai trazer consequências. uma possível solução seria aumentar a carga de frio para o produto sair do sistema de refrigeração com a especificação pretendida. Esta solução não será a mais eficiente, pois se a anomalia se verifica antes do sistema de refrigeração, deve-se atuar no equipamento responsável pelo aumento da temperatura do produto 37.
A falta de isolamento ou a existência de falhas conduz à absorção de calor vindo do exterior através das tubagens, o que vai proporcionar efeitos negativos na funcionalidade do sistema de refrigeração. Por exemplo, se o sistema está a aumentar a sua energia, quer dizer que a temperatura do evaporador é superior à necessária, portanto o consumo de energia no compressor irá aumentar.
Outro aspeto importante é o sistema de distribuição. Toda a energia envolvida para o bombeamento do fluido refrigerante pelo sistema pode contribuir para um gasto ineficiente de energia. é importante que a bomba esteja pronta para operar para cargas de fluido refrigerante diferentes. Em sistemas de bombas com cargas de fluido variáveis é comum usar bombas com variadores eletrónicos de velocidade (VEV). A Tabela 4.1 indica as possíveis poupanças com a utilização de VEV para motores de 5,5 kW e 18,5 kW, que operam 8000 horas por ano.
Tabela 4.1 – Poupanças resultantes da instalação de VEV 36, operando 8000 h/ano
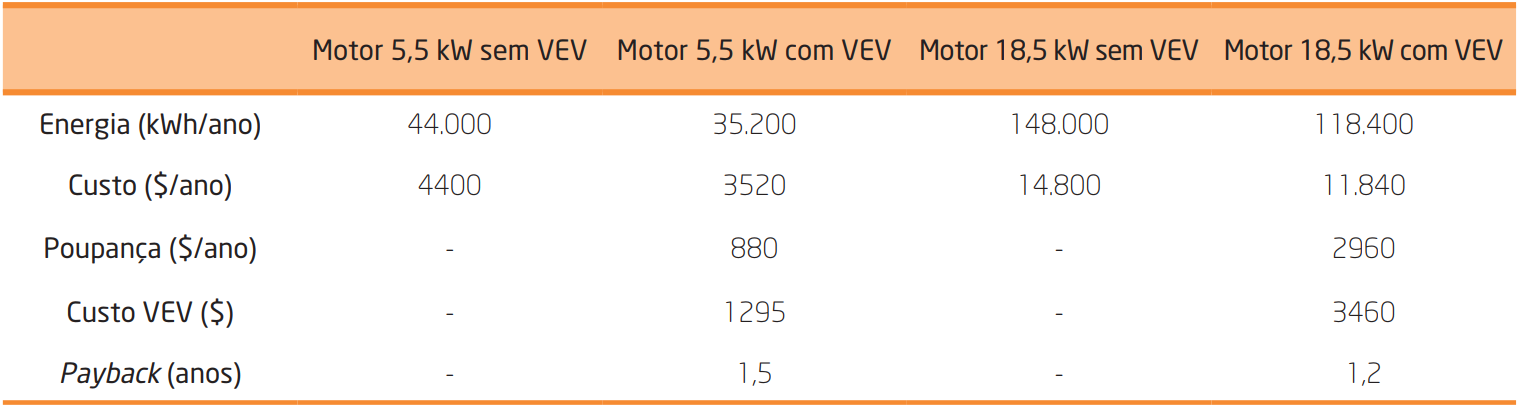
![]() |
A utilização de bombas com VEV resulta numa redução do consumo de energia de 20%. |
Todo o sistema de refrigeração deve estar bem controlado, para um melhor entendimento sobre como o sistema está a operar. um sistema de controlo eficiente e fidedigno pode ajudar numa rápida atuação sobre qualquer problema que ocorra com o condensador, compressor e evaporador.
A manutenção do sistema também é de extrema importância. Para evitar uma reduzida transferência de calor, o operador deve ser capaz de efetuar testes de desempenho, tal como é recomendado pelos fabricantes 37.
As falhas no compressor podem por vezes ser difíceis de identificar, embora estejam relacionadas com falhas mecânicas ou com bloqueios internos. os níveis de óleo e fugas devem ser verificados 37.
Falhas com as válvulas de expansão, estão geralmente relacionadas com o facto de estas abrirem ou fecharem quando não devem, aumentando a pressão à entrada do compressor.
Monitorizar a temperatura ótima do condensador é bastante importante para tornar eficiente a operação. os problemas relacionados com o condensador são devido a uma transferência de calor pobre. A presença de ar e não-condensáveis no fluido refrigerante vão aumentar a temperatura de condensação e diminuir a eficiência 37.
A Tabela 4.2 apresenta um resumo do impacto de cada medida na eficiência energética do sistema de refrigeração
Tabela 4.2 – Resumo das economias por abordagem
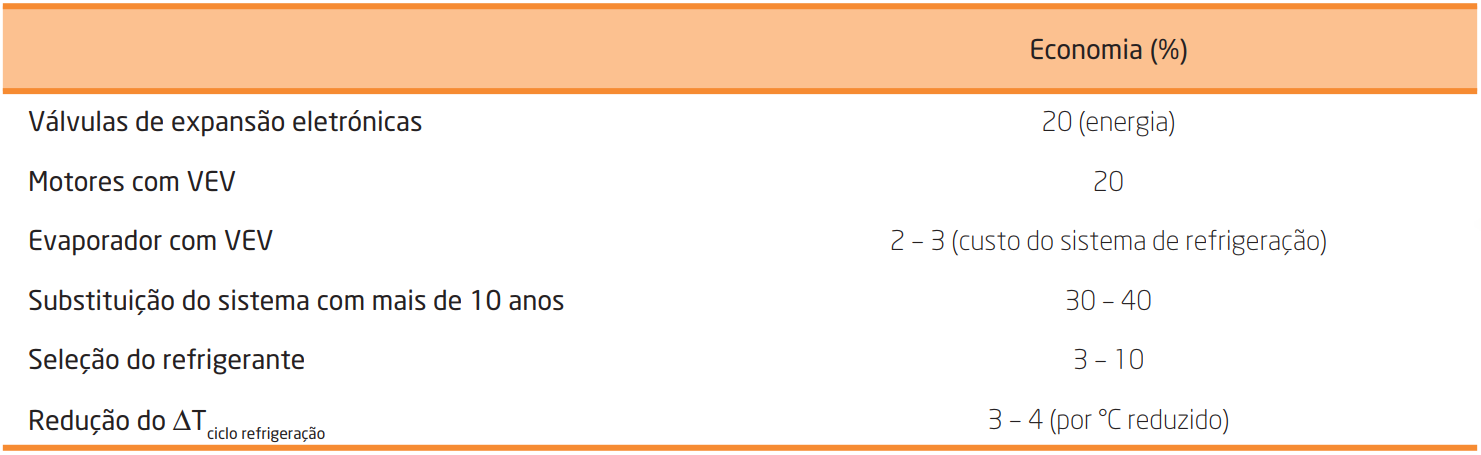
Em vez de um motor elétrico, é possível utilizar um motor a gasolina para transmitir energia mecânica ao compressor de um sistema de refrigeração. Este sistema já foi testado na produção de gelo, na indústria alimentar e na indústria química. Além disso, um sistema de refrigeração com motor a gasolina pode ter um refrigerador de absorção (absorption chiller) acoplado.
![]() |
A utilização de um motor a gasolina permite poupar até 52% do consumo de energia primária inicial. Acoplado com um refrigerador de absorção essa economia pode atingir os 77%. |
![]() |
O motor a gasolina aumenta as emissões de NOx, podendo implicar a implementação de medidas extra para a diminuição dessas emissões. |
![]() |
Os sistemas com e sem refrigeração de absorção necessitam de investimentos consideráveis, tendo períodos de payback que atingem os 4 anos e os 2 anos, respetivamente. |
4.3.1.2 Seleção de equipamentos
Geralmente, o compressor é o grande consumidor de energia no sistema de refrigeração, tornando-se importante escolher o compressor adequado à carga.
Tabela 4.3 – Valores típicos de eficiência de compressores
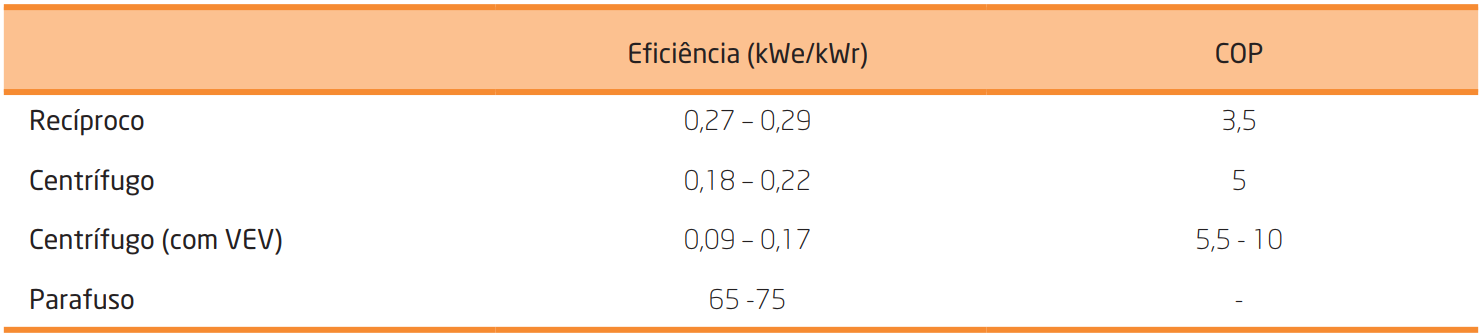
O condensador e o evaporador devem ser dimensionados de forma a obter a menor temperatura de condensação (origina menor consumo de energia) e a maior temperatura de evaporação.
A diferença entre a temperatura de evaporação e condensação está diretamente relacionada com o coeficiente de desempenho do sistema de refrigeração. o coeficiente de performance do sistema de refrigeração (COP) fornece o valor de frio que se consegue produzir em função do valor de energia gasta para o produzir.
O COP será tanto maior quando menor for a diferença entre a temperatura do evaporador e a do condensador (∆Tciclo refrigeração).
O dimensionamento do evaporador deve ser feito para cada processo específico, de modo a minimizar todas as perdas que estão associadas a este tipo de equipamento.
4.3.2 Termoacumulação ou Armazenamento de Energia Térmica
A termoacumulação é uma tecnologia “antiga” que tem vindo a ser redescoberta para aplicações industriais (p. ex., indústria alimentar). Esta tecnologia permite a produção de gelo nos períodos em que a eletricidade é mais barata (períodos de vazio) e o armazenamento do gelo em ice ponds, até que este possa ser utilizado para refrigeração. Com sistemas de armazenamento de energia térmica é possível responder às necessidades dos vários setores – comercial, industrial e utilidades – em aplicações como aquecimento de espaços e águas domésticas, refrigeração e ar condicionado 38.
A acumulação de energia térmica é um princípio de conservação temporária de energia para posterior utilização. Alguns exemplos de sistemas de armazenamento de energia térmica são:
- Acumulação de energia solar para utilização noturna;
- Armazenamento de frio no inverno para o arrefecimento na época do verão;
- Armazenamento de calor no verão para o aquecimento de espaços no inverno;
- Armazenamento nas horas de baixas tarifas de eletricidade (refrigeradores a funcionar durante a noite para depois o fluido refrigerante ser utilizado na rede industrial somente quando existir procura).
Na Figura 4.6 encontram-se esquematizados os dois tipos de armazenamento de energia térmica. Existem duas vertentes de calor armazenado: calor sensível e calor latente.
O processo de armazenamento de energia térmica pode ser obtido por arrefecimento ou aquecimento de uma substância (calor sensível), ou por mudança de fase desta, quer por fusão ou vaporização (calor latente), ficando a energia disponível aquando da ocorrência do processo inverso. Se o armazenamento for feito através do aumento ou diminuição da temperatura do material é denominado armazenamento de calor sensível 38.
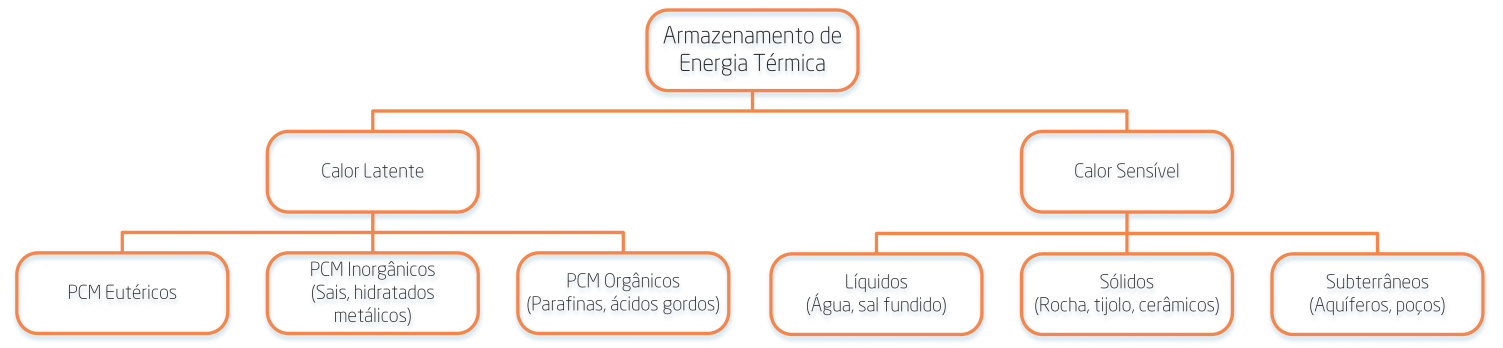
Figura 4.6 – Tipos de armazenamento de energia térmica
Outra característica que distingue os diferentes sistemas de armazenamento de energia térmica é a duração de armazenamento: curta, média ou longa.
O armazenamento por um curto período de tempo é utilizado para resolver cargas de potência de pico, desde durações de umas horas até ao máximo de um dia, com vista à redução da dimensão dos sistemas e ao aproveitamento da estrutura diária das tarifas de energia. Este tipo de armazenamento é denominado armazenamento diurno.
O armazenamento de médio ou longo período de tempo é recomendado quando há a possibilidade do calor residual e das cargas sazonais de energia serem transferidos com um atraso desde algumas semanas até meses.
A principal característica de um sistema sazonal de armazenamento é a grande capacidade que esta solicita. As perdas térmicas revelam-se significativas nos sistemas de longo prazo, por esta razão são necessários mais cuidados para preveni-las num sistema sazonal por comparação com um sistema diurno.
Os custos associados ao tamanho e ao isolamento dos sistemas de armazenamento sazonal impedem que a maior parte destes sejam económicos. Os sistemas de armazenamento diurnos apresentam vantagens, tais como, o capital de investimento, baixas perdas energéticas e unidades mais pequenas. os sistemas anuais apresentam maiores dimensões, embora sejam ideais para parques industriais 38.
Existem já empresas que gerem, de forma centralizada em zonas restritas habitacionais e de serviços, sistemas de climatização para o aquecimento central dos edifícios, a sua refrigeração e o aquecimento das águas sanitárias destes.
As centrais podem funcionar com um sistema de trigeração, isto é, a partir da mesma fonte energética (gás natural) produzem em simultâneo energia elétrica, calor e frio.
As principais vantagens da rede urbana de frio e calor é a redução do consumo de energia primária e das emissões de dió-
xido de carbono.
A distribuição da energia térmica é efetuada com água arrefecida ou aquecida e processa-se através de uma rede de tubagens. A transferência de energia entre a rede de distribuição e os edifícios é efetuada em subestações existentes nos edifícios através de permutadores de calor.
- 25 European Commission, “Reference Document on Best Available Techniques for Energy Efficiency”, Fevereiro 2009.
- 26 ADENE, “Medidas de Eficiência - Indústria”
- 28 P. Radgen e E. Blaustein, “Compressed Air Systems in the European Union – Energy, Emissions, Savings Potential and Policy Actions”, 2001.
- 32 N. Martin, E. Worrell, M. Ruth, l. Price, R. N. Elliott, A. M. Shipley e J. Thorne, Emerging energy-efficient industrial technologies, eScholarship - University of California, 2010.
- 33 Industrial Heating, “Improving Energy Efficiency with Recuperative and Regenerative Burners”
- 34 H. Tsuji, A. Gupta, T. Hasegawa, M. Katsuki, K. Kishimoto e M. Morita, High Temperature Air Combustion: From Energy Conservation to Pollution Reduction, CRC Press, 2002
- 35 M. A. Boles e Y. A. çengel, “Thermodynamics: An Engineering Approach”, Seventh Edition ed., Mc Graw Hill, 2011.
- 36 S. G. victoria, “Energy Efficiency Best Practice Guide: Industrial Refrigeration”, Australia, 2009.
- 37 W. Stoecker, “Industrial Refrigeration Handbook”, McGraw-Hill, 1998.
- 38 I.Dinçer e M. Rosen, “Thermal Energy Storage: Systems and Applications”, Wiley, 2011.